What’s New in CATIA V5 Release V5-6R2019 – MACHINING
Posted By: Remy Boutin
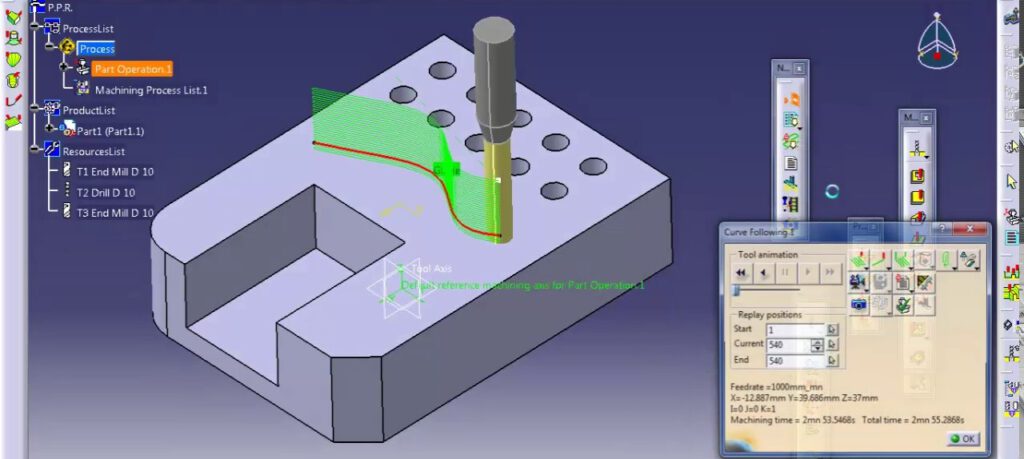
Design change
When analyzing the geometry specified on a Machining Operation, you can now use new commands to:
- Reframe the main viewer on the selected geometry
- Center the specification tree on the selected geometry
These commands are available in the Geometry Analyzer dialog box.
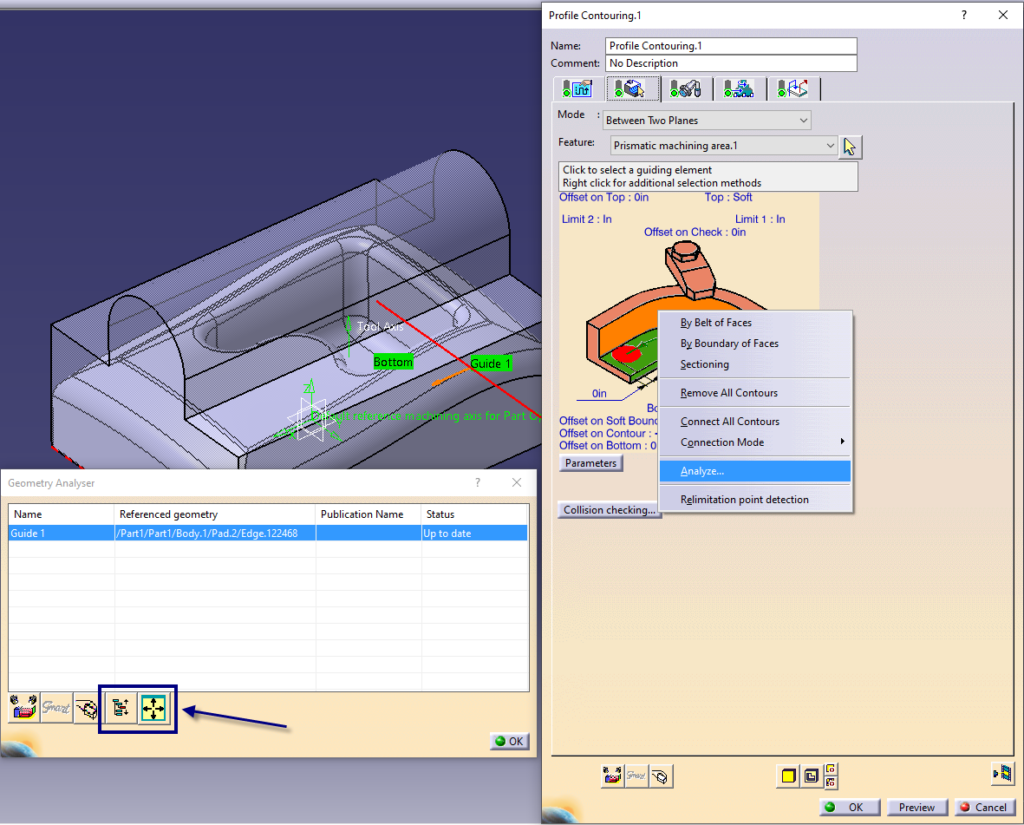
Resources
When you modify the total length value (ST) of a tool assembly, you can now select the Assembly total length linked to tool gage check box to keep the height value of the last stage of the tool holder during modification.
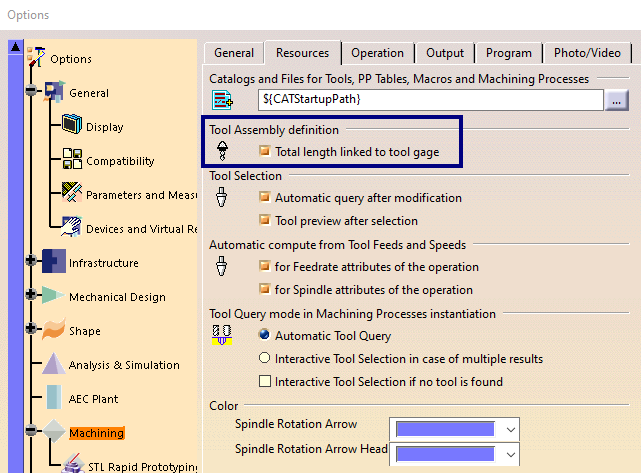
New Functionality
The strategy tab in drilling deep hole operations
There are new parameters available:
- DeepHole LeadIn
- DeepHole LeadOut
- NoRetract Motion
The feedrate tab in drilling deep hole operations
There is a new parameter available:
- DeepHole Feed Reduction
NOTE:
Reducing the feed rate is only available when all drilling operations are designed with MAFs.
To compute the tool path of a deep hole drilling operation, you must force the tool path computation of the manufacturing program and generate the APT source output.
To compute the tool path, you must force the tool path computation of the manufacturing program and generate the APT source output.
Machining Operation dependency is only supported when intermediate stock is used.
Enhanced Functionality
Pocketing, 4-axis pocketing, profile contouring, roughing, spiral milling, multi-axis spiral milling, power machining, cavities roughing, rough turning
Concentric tool path style now supports zig-zag sequencing on a circular pattern.
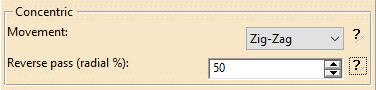
Profile contouring operations
For profile contouring operations, you can now use a concentric tool path to control the tool radial engagement along the trajectory. This allows you to mill hard metal parts facer, to lower wear on cutters and avoid cutter breakage.
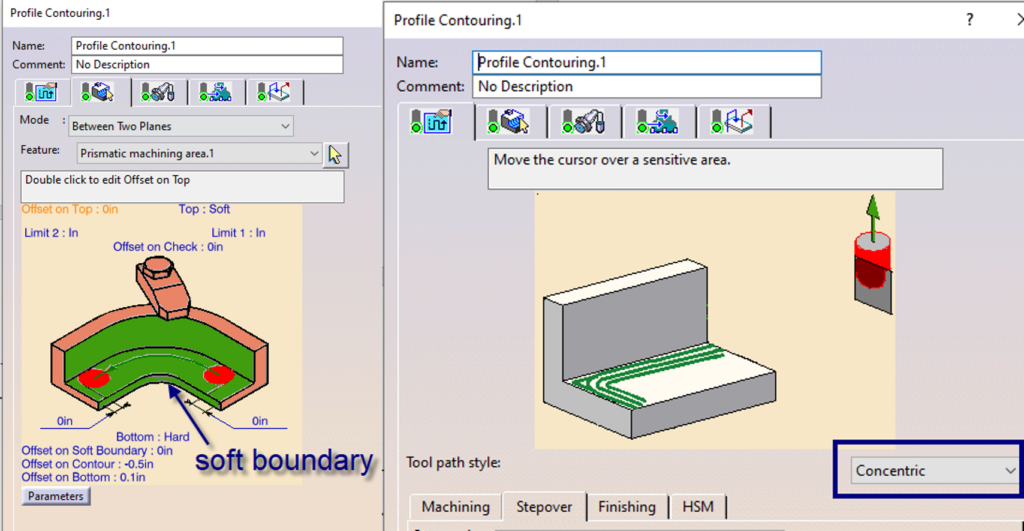
Pocketing and roughing operations
You can now specify the following additional parameters for pocketing operations in Concentric:
- Pattern: Auto, Circular or Dynamic
- Channel width percentage
- Maximum discretization
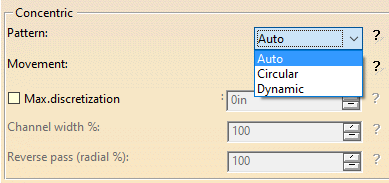
The option “Always stay on bottom” is now available for Pocketing and Roughing operations with Concentric Tool Path Style. Specific clearance and feedrate can be defined for optimized linking motions.
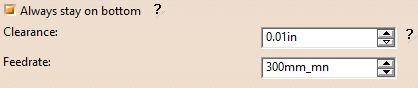
NC Macros Enhancements for ALL Machining Operations
New activate/deactivate behavior
Double click macro line to quickly activate/deactivate.
New copy/paste command
- Copy all motions in one time and paste them in other macro inside the same operation or into another operation
- Compatibility checks are performed when pasted in target
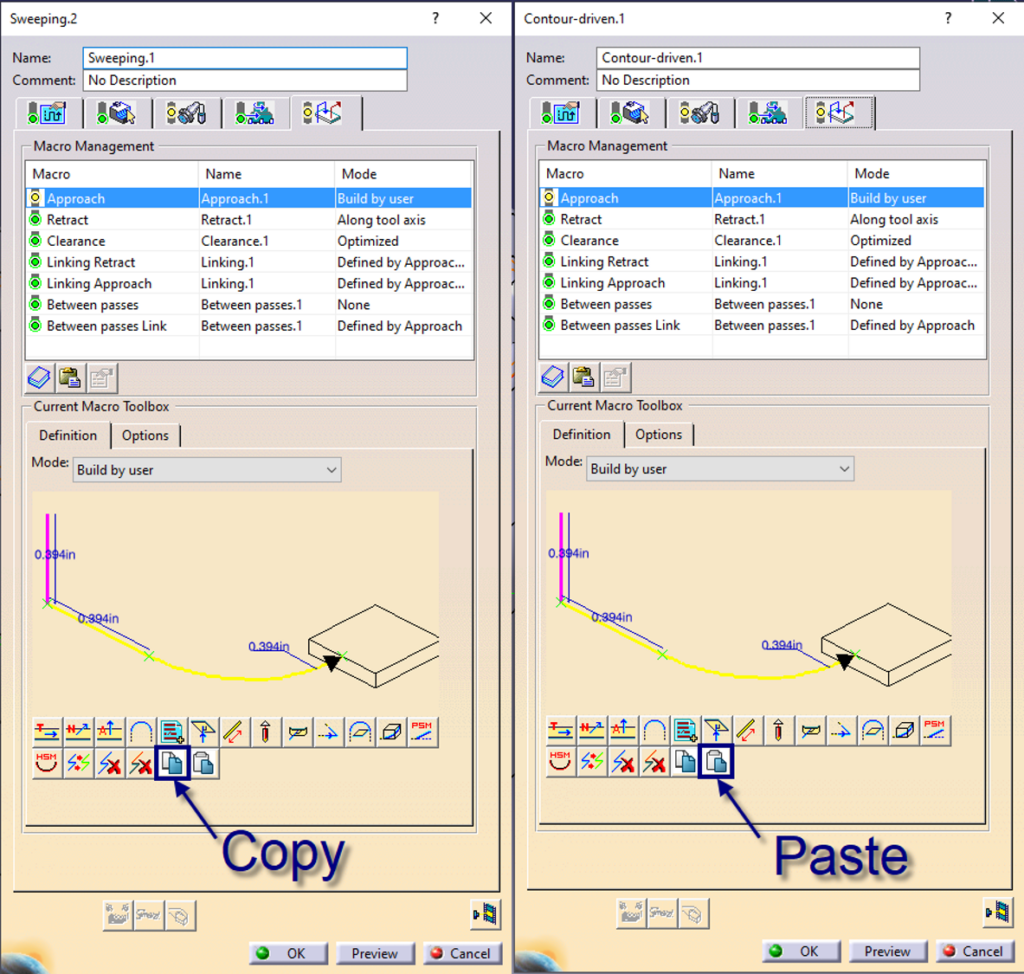