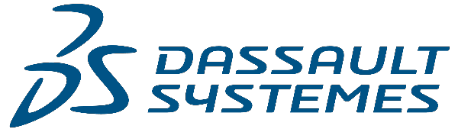
Global teams collaborating with global information and doing so with clarity, confidence and consistency
ENOVIA allows companies to connect online communities to share and collaborate on global product information, ensuring that everyone uses a single version of the truth. ENOVIA is the common collaborative platform for all Dassault Systèmes brands.
Portfolios
Platform Contributor is the entry point to the 3DEXPERIENCE® platform and provides customers with the full technical platform architecture. It contains essential apps for users to collaborate with one another in order to deliver delightful experiences for their ultimate customers.
Description
The 3DEXPERIENCE platform is available on premise and on the cloud and is based upon the powerful and proven V6 architecture. This is critical to ensure a smooth upgrade for existing customers and a smooth initial implementation for new customers in order to benefit from this innovative approach for experience creation.
Change Management saves time and money by enabling companies to efficiently define, standardize and execute change management processes across multiple business functions. Its process methodology covers the complete scope of a change from concept, planning, design, and manufacturing to final product delivery and release.
Description
Increasing business, product and process complexities affect operating margins and are driving companies to find business solutions which foster innovation and improve efficiencies. In most industries today, the complexity and rate at which new products need to be developed has already out-paced the rate at which many companies can produce them. One of the significant bottlenecks in the global product development process is in the identification, analysis, approval and implementation of product changes. As new products are introduced, which often times have market specific functions and options, the change management challenge is compounded.
A key enabler of realizing the benefits of global product development best practices is establishing a standard global change process for all of the business functions involved. Multiple, inefficient, non-standard change processes and systems cause significant delays in product introduction through miscommunication, labor intensive, error prone data entry, and validation of changes across multiple change systems. Companies need to implement a scalable change methodology that can evolve and adapt to global growth strategies.
Change Management enables companies to address a number of key business challenges related to global product development:
- Consolidate and optimize change board meetings and decisions by establishing a unified change process across domains.
- Clearly communicate change decisions across all impacted organizations.
- Improve change visibility and communication between global teams.
- Reduce the time and cost associated with iterative, error prone change orchestration and synchronization scenarios with intelligent change management rules and automation.
While Change Management is offered separately for users that just need to orchestrate the change process, its capabilities are also included with the following ENOVIA® licenses that are used to create product development data:
- Packaging Copy and Artwork Manager
- Packaging Copy and Artwork Designer
- Device Master Record Manager
- Formula Management Enabler
- Product and Specification Engineer
- Product Engineer with New Part Request
- Product Architect
- Product Engineer
- Product Manager
- Quality Document Manager
- Financial Services Manager
More Effectively Leverage Information and IP for Decision Making
Report Generator allows users to execute dynamic reports from the information stored in the 3DEXPERIENCE® platform. Reports can include high-resolution images and intuitive charts to simplify a user’s understanding of complex product data.
Description
Report Generator supports several formats and delivery mechanisms that best suit end users from various parts of the company. As a result, its reports lead to greater participation of users throughout the product development process. In addition, the flexible architecture of Report Generator allows it to be customized or extended as needed to meet unique customer needs. With Customization and Specialization Administrator, Report Generator can execute highly tailored reports. These reports support custom layouts that can be generated in a variety of formats, including HTML, PDF, XML, and Microsoft Excel (via SpreadsheetML or CSV). This delivers information from the 3DEXPERIENCE system to the users that need it, in the format that matches their needs, when they need it.
Taking the concept of “what you need, when you need it” one-step further, Report Generator supports the use of templates to deploy reports in other products, or use them as a model for creating new reports. Report Generator also supports style sheets, which may be shared across reports, allowing companies to create reports with a polished professional look.
System performance is important for all report generation. Report Generator provides control of the queuing of the report generation process, and uses “queue agents” to support distributing report generating processes across multiple servers. Once generated, reports can be delivered for viewing online, stored in a business object for viewing later, or as a file for external distribution, by way of email, FTP, or using the Java Message Service (JMS).
Users can invoke Report Generator through its user interface, via a URL, or from triggered events such as lifecycle promotions. In addition, pre- and post-processing adds flexibility to collect information on a screen prior to running the report, or adding a watermark to the report after it has been generated.
AutoVue 2D Viewer allows CAD and non-CAD users to view, markup, and collaborate synchronously or asynchronously on design data through use of the 3DEXPERIENCE® platform.
Description
The ability to share information across the enterprise is a must for today’s global enterprises. AutoVue 2D Viewer provides an automated, electronic and secure approach for document and 2D CAD viewing. It makes it possible to review and collaborate without the need for access to the native application that generated the documents.
AutoVue 3D Viewer allows CAD and non-CAD users to view, markup, and collaborate synchronously or asynchronously on design data through use of the 3DEXPERIENCE® platform.
Description
The ability to share information across the enterprise is a must for today’s global enterprises. AutoVue 3D Viewer provides an automated, electronic and secure approach for document and CAD viewing. It makes it possible to review and collaborate without the need for access to the native application that generated the documents.
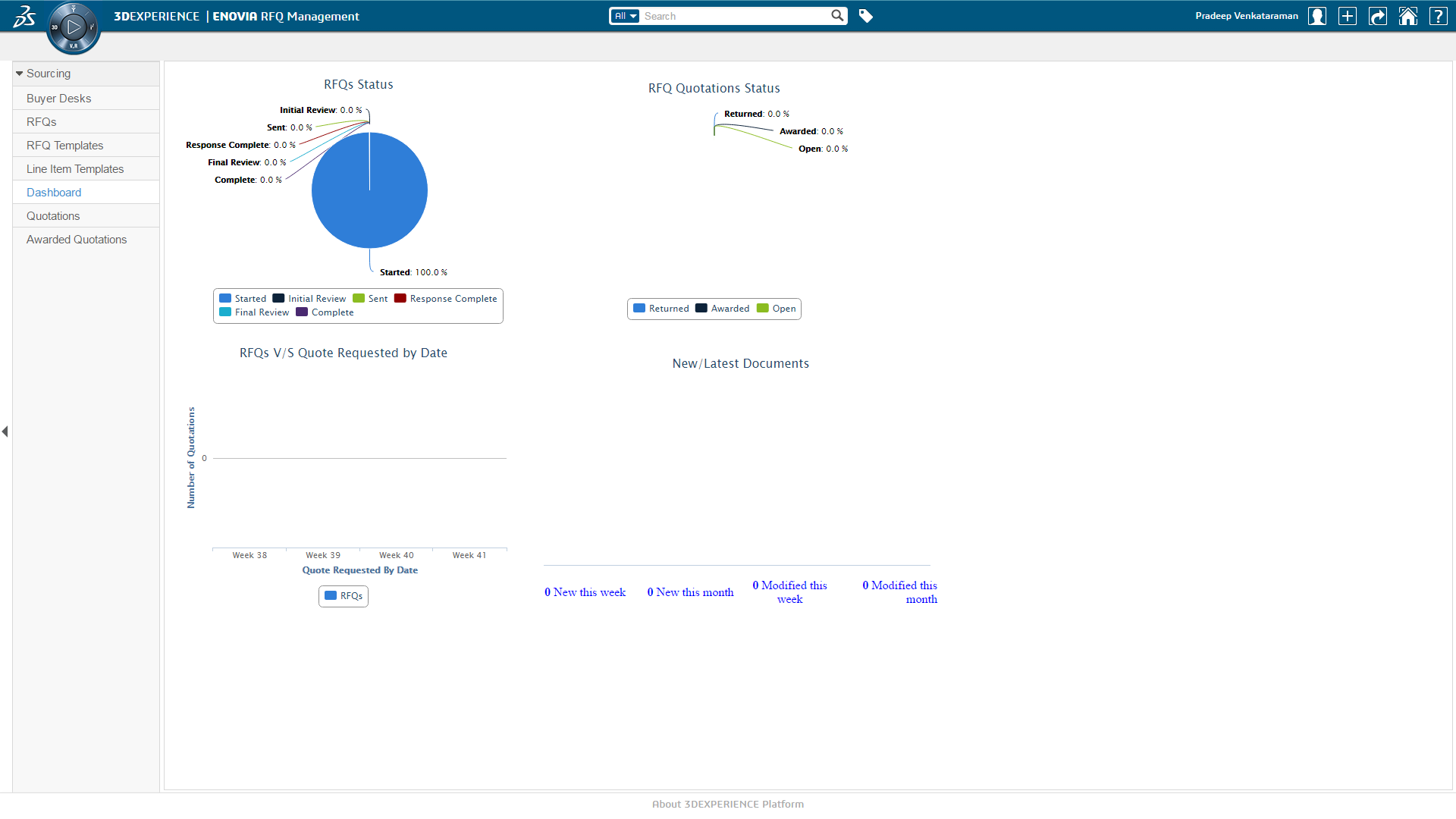
Drive profit with better and faster sourcing practices.
Description
RFQ Manager provides online request-for-quote (RFQ) management for sourcing engineered products and services. When used with Bid Manager, suppliers securely become an extension of a company’s engineering organization, for better and faster sourcing practices that drive key profit, cost, and time-saving decisions.
Key Benefits
Shorten Response Times
Sourcing process that involves a collaborative environment with connection to information, data, and decisions in real time.
Improve Product Development
Collaborate directly with buyer organization during design & development reducing reliance on data exchange. Ensures security of Supplier IP while delivering value added capabilities like real-time DMU and design in configured context.
Reduce Product Production Delays
Enable participation in project management framework to ensure compatibility, increased visibility, and early detection of risks, issues, and opportunities.
Generate More Value from Suppliers
Manage deliverables in term of planning, quality and cost to improve product costs without compromising quality.
Global Engineering Manufacturing Management
Enable bill of material management across the product lifecycle—from as-designed to as-manufactured, as-planned, and all the way to as-built and as-serviced stages.
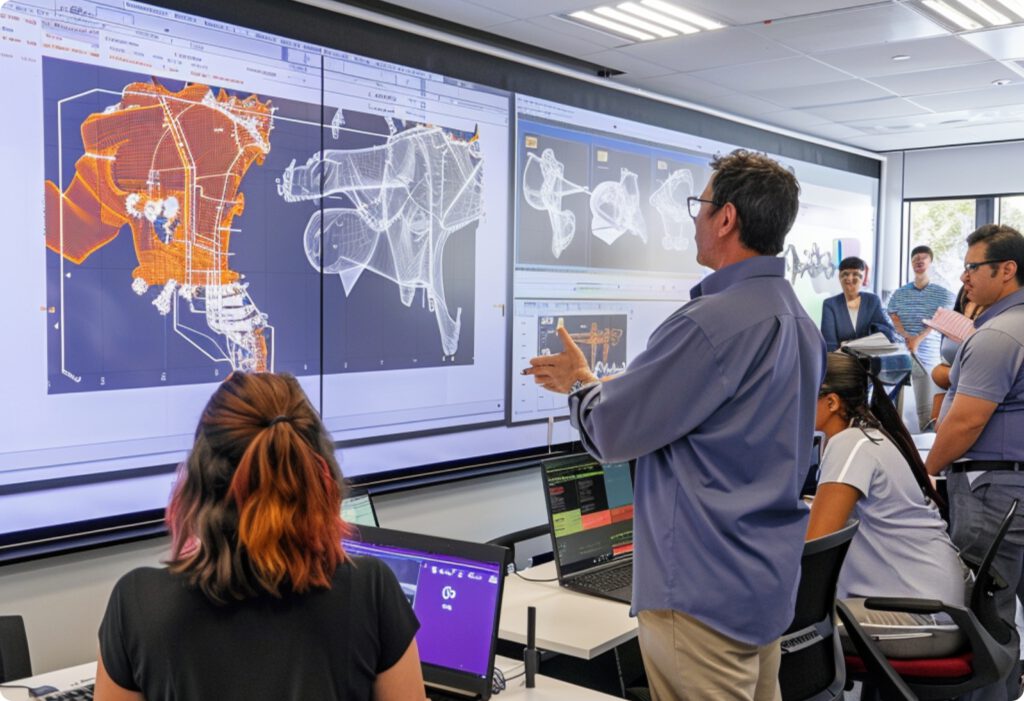
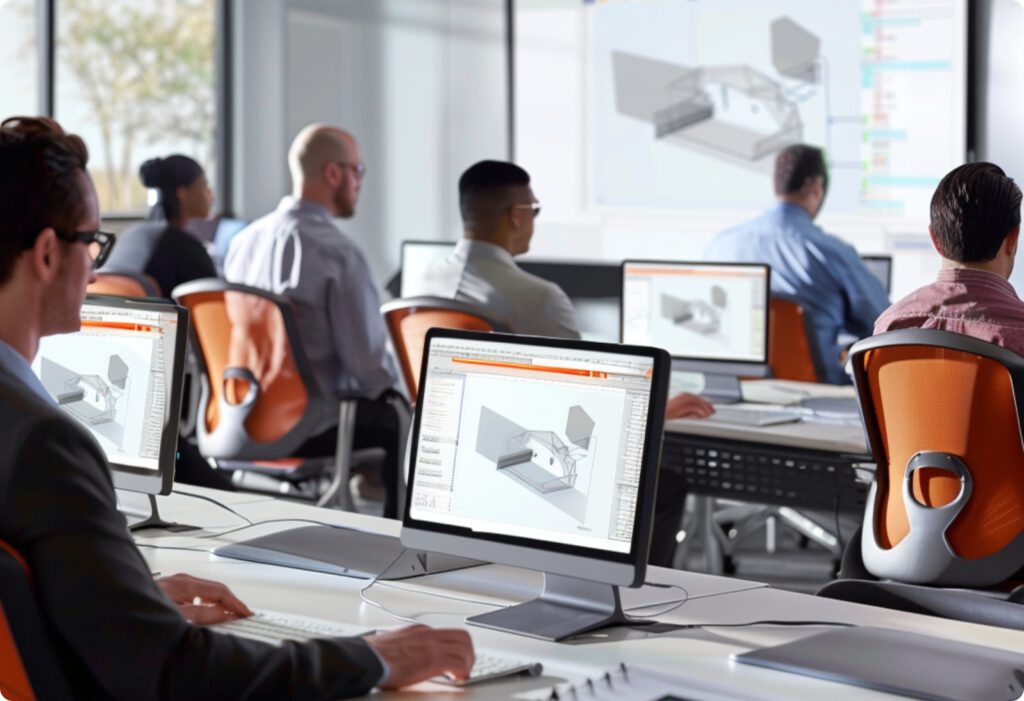
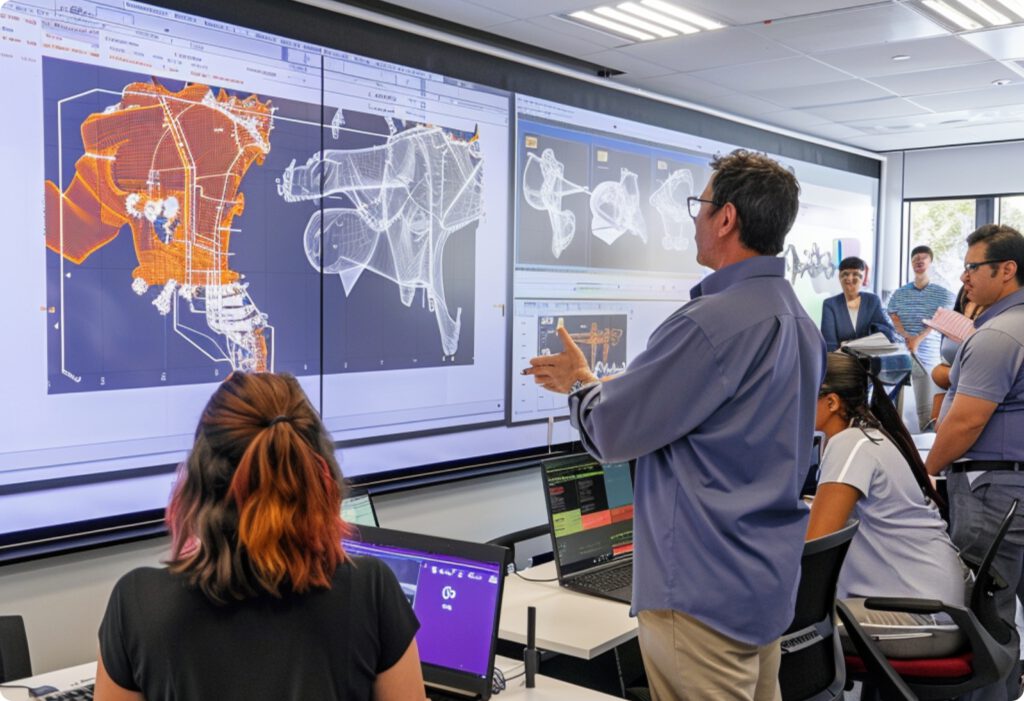
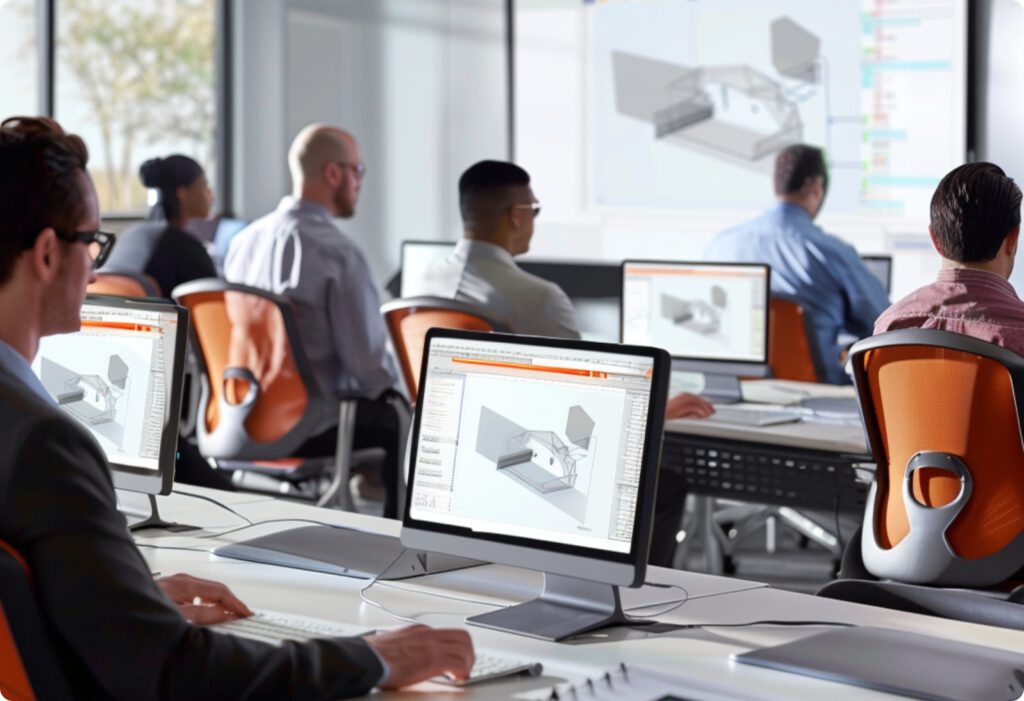
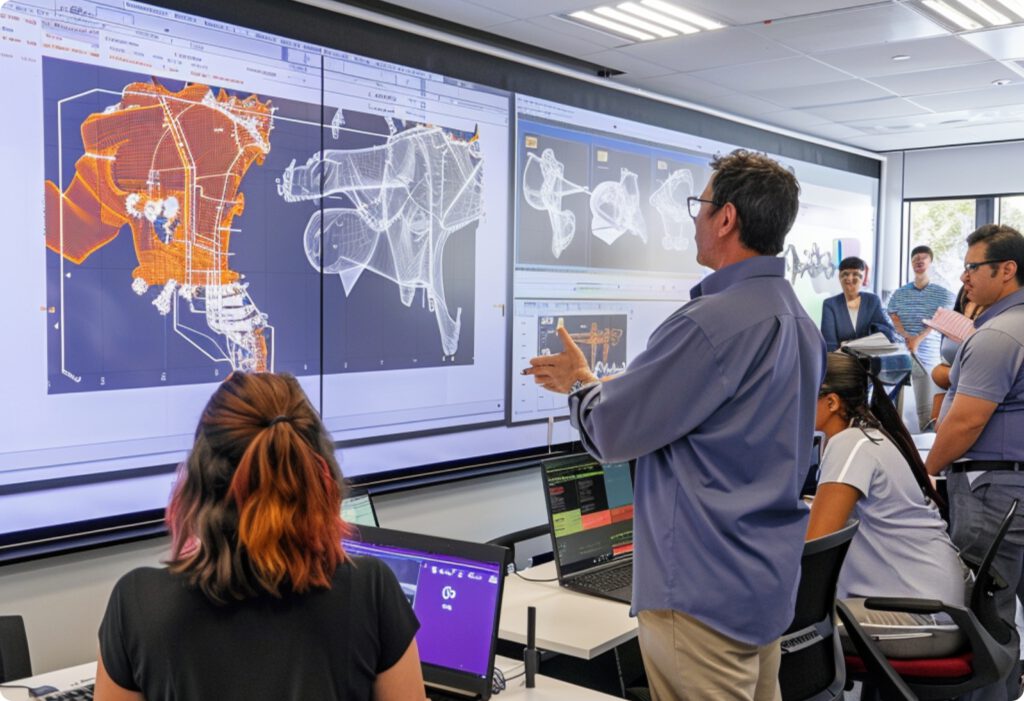
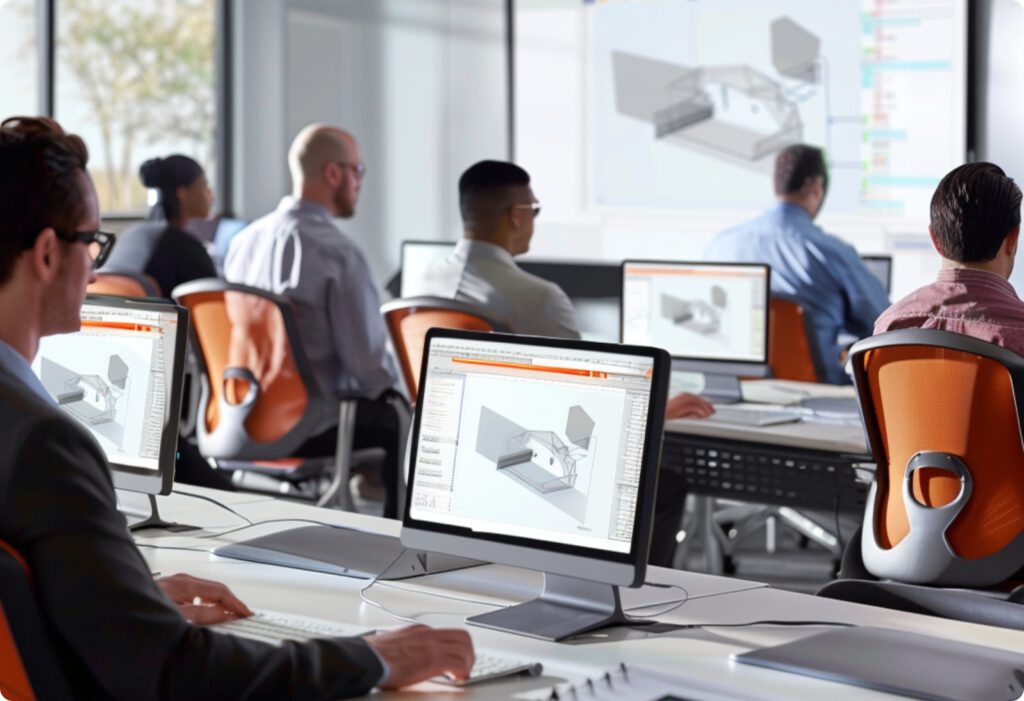
Product Planning and Programs
Imagine your company has 20 concurrent projects, 1500 engineers and 150 suppliers. Meanwhile, your engineers are introducing 5000 new parts per year! With Product Planning and Program Management solutions from ENOVIA, clients can precisely orchestrate even the most complex of processes.
ENOVIA Product Planning and Program Management delivers “invisible governance” which provides the ability to identify potential issues and risks before they fully manifest. With invisible governance, you can drive project updates with deliverable status.
Project Manager allows companies to target zero delays with their product planning and development processes to achieve optimal cycle times within scope, capacity and resource constraints. Organizations can concentrate on the most profitable products while standardizing on best-in-class business processes across the extended enterprise.
Description
All companies are faced with ever-shrinking product lifecycles in order to timely satisfy the diverging needs of global markets. This has resulted in an increase number of concurrent product development programs, which necessitates adoption of concurrent engineering methods. However, this also increases complexity due to the parallel activity of various functional teams. Coordinating the various functional teams to prevent overloaded resources and bottlenecks is critical for optimizing cycle time.
If one looks at a classic product profit curve, it is evident why cycle time optimization is so important. All products incur upfront costs before revenue is generated. As a product grows and matures, revenue should make up for the upfront costs and profits should nicely accumulate. Towards the end of the product lifecycle, companies try to exit before revenues decrease below costs and profits erode. If product development management processes are adopted that allow cycle times to shrink then the product launch occurs sooner, which allows revenue to also be obtained sooner. In effect, this profit curve shifts left and can even increase because a company is able to capitalize on market opportunities sooner before competition can react.
Project Manager uniquely accomplishes zero delays by linking product development data to project execution. In effect, project management becomes data-driven by being linked with the product portfolio. When the two processes are disconnected with different technologies, there are multiple projects being defined and tracked, but they are not grounded in the reality of the product data that is being created as part of the project. As a result, it is difficult to understand or contain execution issues related to product planning decisions or portfolio issues related to execution problems.
With Project Manager and the 3DEXPERIENCE® platform it is possible to permanently associate the definition and development of the product portfolio with the tracking of the projects used to govern it. The implications of portfolio decisions can be quickly assessed against the project schedule. As a result, a project manager is taking action to resolve issues with a full understanding of the impact to the product portfolio.
Successful execution of contract-based programs means managing volumes of information to efficiently meet all contractual obligations. Contract-based Program Manager integrates all critical data and program information into one consistent whole to make it more understandable and provides a permanent reference and program “memory” to inform new team members.
Description
Tracking, reporting and communicating information involves teams of people across multiple functions and organizations. Programs succeed or fail on their ability to communicate very reliably with all the team members over long periods of time. Contract-based Program Manager utilizes the 3DEXPERIENCE® platform to make product content available to users more securely. Through project pipeline dashboards, Contract-based Program Manager provides real-time visibility into a project’s status in terms of schedule, resources, costs, and benefits. Users can create and access 3DEXPERIENCE data from the most popular Microsoft applications, including Word®, Excel®, PowerPoint®, Outlook®, Project, Windows Explorer, and Windows Desktop Search.
Contract-based Program Manager includes capabilities to support a single environment with a consistent look-and-feel and enterprise security for these functional disciplines:
- Contracts Management
- Sub-contracts Management
- Data Management
- Program Management
- Program Planning & Control (PP&C)
- System Engineering
Performance-to-contract is greatly improved when all contract requirements are visible to the entire team. Using one system to bring together the core processes of these functional disciplines provides the ability to improve overall performance of program execution and delivery-to-contract. Contract-based Program Manager enables users to:
- Capture contracts and their associated work-breakdown elements in line-item detail to ensure complete assignment, scheduling and proper execution.
- Work-breakdown elements reference the scheduled tasks required to complete the work assigned.
- Link projects with critical milestones and deliverables to the contracts and baseline product architectures.
- Link hardware and software deliverables to schedule tasks.
- Capture contract requirements for data delivery with the Contract Data Requirements List (CDRL) and Subcontract Data Requirements List (SDRL).
- Generate and schedule submittal tasks and link actual data deliverables documents for assignment and future completion.
In order to align downstream product development with the contract requirements, the complimentary Requirement Manager should be used to capture, share and manage technical requirements.
Involve a Broader Community of Stakeholders in Key Project and Program
Contract Deliverable Manager provides a collaborative environment for users to access, manage and deliver contract documentation and deliverables (i.e. “Submittals”) according to their task assignments.
Description
Companies can no longer rely on manually collecting project status. Time spent searching for and transforming data and conducting physical meetings with numerous attendees must be avoided and eliminated. Contract Deliverable Manager achieves this by making the updating of project task status part of the same 3DEXPERIENCE® system used to develop and manage the content delivered to fulfill the project task. In effect, project management capabilities are put directly in the context of the tools of users so reporting status is not seen as a burden. Reliance on manual collection of status is reduced or eliminated.
When users can report task status via their normal activities, the concept of “Invisible Governance” is enabled. The alternative to invisible governance is team members communicating status through informal approaches like e-mail, or program managers being forced to manually collect and compile status updates. This is effort intensive and very time consuming. Further, the information is always out-of-date since progress goes on immediately after status is reported. Inefficiency and poor/late data makes effective decisions a matter or intuition rather than data-driven. Contract Deliverable Managereliminates these issues.
Contract Deliverable Manager provides users visibility to their contract and project assignments and allows them to create risks, issues and opportunities. Users collaborate through shared folders and documents for the deliverables to define status, approve and review.
Ensure Completion of Design Control Deliverables Across Enterprise Regulated Value Streams
Project and DHF Manager manages new product development design projects, activities and content with creation of the device design history file to satisfy regulatory standards and good manufacturing practices for design control.
Description
All companies are faced with ever-shrinking product lifecycles in order to timely satisfy the diverging needs of global markets. This has resulted in an increase number of concurrent product development programs, which necessitates adoption of concurrent engineering methods. However, this also increases complexity due to the parallel activity of various functional teams. Coordinating the various functional teams to prevent overloaded resources and bottlenecks is critical for optimizing cycle time. This becomes even more challenging in industries that demand product development to comply with government regulations.
Project and DHF Manager uniquely accomplishes zero delays by linking product development data to design project execution. In effect, design project management becomes data-driven by being linked with the product portfolio and the design content that regulatory agencies demand. When the two processes are disconnected with different technologies, there are multiple design projects being tracked, but they are not grounded in the reality of the product data that is created. Additionally, with disconnected processes it is not clear if the design content needed for regulatory agencies is being produced to ensure an on-time product launch.
Project and DHF Manager dramatically increases productivity globally by executing design projects and programs with real-time design information updates via automated synchronization of design artifacts to the DHF. This automated synchronization allows the design project or program manager to focus on high-value activities rather than tracking down design status. With Project and DHF Manager, companies can provide global teams with the accurate, real-time design information they need to keep design projects on track in response to ever-shrinking product lifecycles. Project and DHF Manager provides management with real-time visibility into a design project’s status in terms of overall schedule, phases, gates, and resources.
Project and DHF Manager is implemented in the medical device industry, which places a priority on design quality. Poor design quality can literally be a matter of life and death in its worst case. Because of the risks involved in the development of novel medical devices, due diligence is of the upmost importance in terms of quality control measures. These competing priorities—quality and time-to-market— must be well managed through a careful process in order to reduce the risks inherent in the medical device industry.
Program Cost Manager enables the collection, analysis and collaboration of contract-based program, project costs and schedules. It manages high-risk, high-cost, or long-lead projects through industry-standard guidelines (EIA-748). This standard is required in government contracting and is the accepted standard in the Aerospace & Defense, Energy, Architecture & Construction, and Marine & Offshore industries.
Description
With Program Cost Manager it is possible for a company to automate resource planning activities for cost and schedule and institutionalize its best practices for various project types according to an industry standard (EIA-748). Its collaborative capabilities dramatically increase the visibility of current earned value and schedule value performance information to better make decisions regarding resources, schedule, and budgeting.
Program Cost Manager can provide global teams with the accurate, real-time information they need to keep projects on track and respond better. Through standard metrics aligned with the Gold Card, Program Cost Manager provides visibility into a project’s status in terms of overall schedule, resources, and costs for planning and actual evaluation. These standards support a fuller view to the project than just the status as you can forecast the Estimate at Completion and other factors to help recover or adjust a project plan or define future needs for resources. These data and proper tracking of the variances provides the ability to greatly improved overall performance of projects and delivery-to-contract.
Broaden Stakeholder Participation in Sourcing to Improve Global Sourcing Performance
Collection Sourcing Manager seamlessly connects global sourcing and production offices to brand and retail headquarters. It enables enhanced collaboration, process control, and risk management within the sourcing and pre-production processes. A broader user base from within and outside of the organization can now participate in the full sourcing process to ensure compliance with corporate growth, business, and financial goals within their global sourcing strategies.
Description
Collection Sourcing Manager provides the planning, visibility and checking needed to manage sourcing in a global and competitive environment. Collection Sourcing Manager allows sourcing teams to manage the vendor base for materials and finished goods. It also allows sourcing teams to work with merchandising teams in understanding forecasted volumes, and creating a plan to source these products with their vendors. They continue to work with product development teams in sampling and costing materials and products, and eventually place products optimally across the supplier base, improving gross margins and markups. As products are placed, sourcing teams have the ability to check the allocation of placed products against the planned volumes assigned to each vendor. This allows visibility to over allocated vendors, as well as vendors that still have capacity available. These discrepancies can then be corrected by sourcing teams easily. Product volumes can be further allocated by channel, delivery and colorway. Sourcing teams can continue to monitor the delivery and use of bulk materials, as well as the timely production of products.