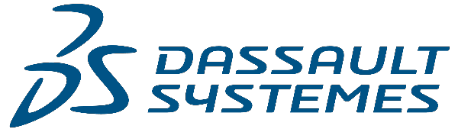
Enhance the real-world performance of your products
Scalable and robust realistic simulation accelerates innovation by enabling engineers to explore and improve real-world product performance in a virtual environment. By using SIMULIA and ABAQUS product development, teams are able to reduce the time and costs of physical prototypes while improving product reliability and safety.
Portfolios
SIMULIA Core Products
SIMULIA makes virtual testing a standard business practice that improves product performance, reduces physical prototypes, and drives innovation.
Reveal the full potential of realistic simulation and use the “Power of the Portfolio” technologies to move from simulate to innovate.
With one purchase, Extended Packaging provides a flexible token pool to access the following capabilities:
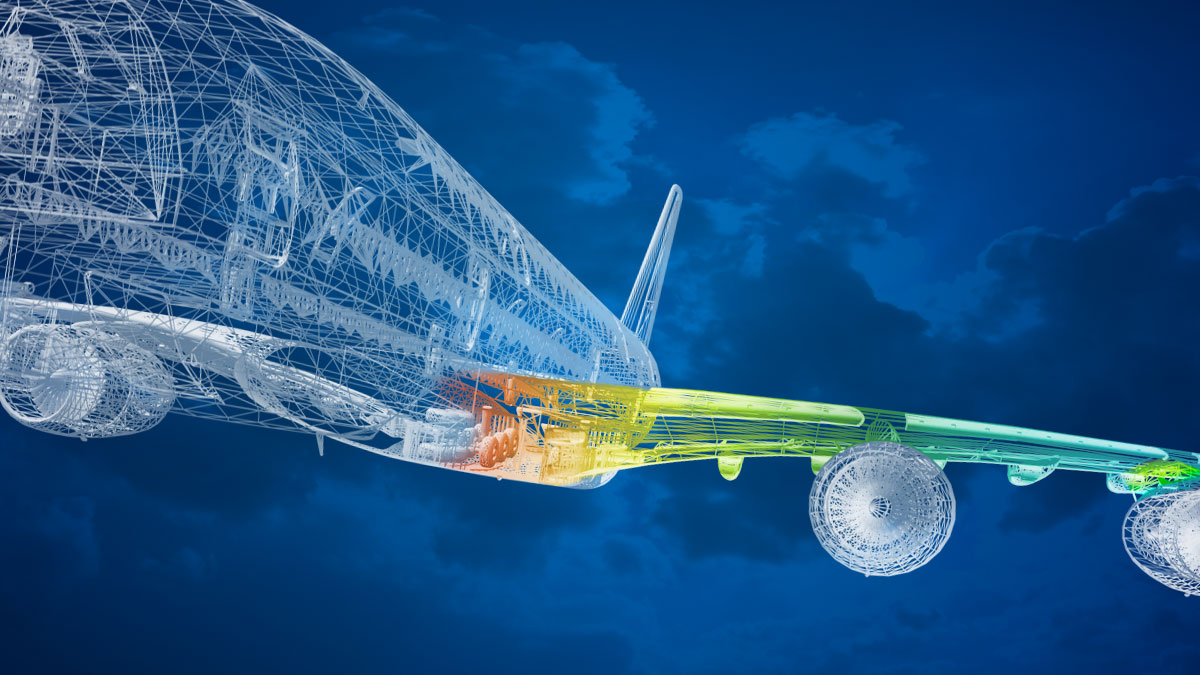
Today, product simulation is often being performed by engineering groups using niche simulation tools from different vendors to simulate various design attributes. The use of multiple vendor software products creates inefficiencies and increases costs. SIMULIA delivers a scalable suite of unified analysis products that allow all users, regardless of their simulation expertise or domain focus, to collaborate and seamlessly share simulation data and approved methods without loss of information fidelity.
The Abaqus Unified FEA product suite offers powerful and complete solutions for both routine and sophisticated engineering problems covering a vast spectrum of industrial applications. In the automotive industry, engineering workgroups are able to consider full vehicle loads, dynamic vibration, multibody systems, impact/crash, nonlinear static, thermal coupling, and acoustic-structural coupling using a common model data structure and integrated solver technology.
Best-in-class companies are taking advantage of Abaqus Unified FEA to consolidate their processes and tools, reduce costs and inefficiencies, and gain a competitive advantage.
Durability Analysis Software for Finite Element Models
Industry is putting increasing pressure on manufacturers to use less material to deliver lightweight but stronger components, lower warranty and recall costs and all in less time. Many companies use advanced finite element analysis to calculate design stresses, but the fatigue analysis is often still done by manually picking stress points for spreadsheet analysis. This is time-consuming and unreliable because it is easy to miss failure locations.
The fe-safe suite of software is world-leading technology for durability analysis from FEA, directly interfacing to all major FEA suites (Abaqus, ANSYS, Nastran (MSC, NEi, NX), Pro/Mechanica) and its capabilities have been developed to meet the most demanding industry applications.
fe-safe was the first commercially available fatigue analysis software to focus on modern multiaxial strain-based fatigue methods and it continues to set the benchmark for fatigue analysis software.
fe-safe is included in Extended Packaging, allowing unified access to all solution technologies within the portfolio through a single token pool.
The fe-safe suite provides:
- fe-safe: Accurate, reliable multiaxial fatigue analysis, regardless of the complexity of your loadings and model
- fe-safe/Rubber: Unique, leading-edge technology for the fatigue analysis of elastomers
- Verity Module in fe-safe: The original, patented Verity® Structural Stress Method for seam, structural and spot welded joints
- fe-safe/TURBOlife: Thermomechanical fatigue analysis with unique capabilities for creep-fatigue interaction
- Smooth workflow between the SIMULIA portfolio of products: Abaqus, Isight and Tosca
Regardless of the complexity of your fatigue analysis, fe-safe fits smoothly into your design process, enabling you to develop products that are designed for durability.
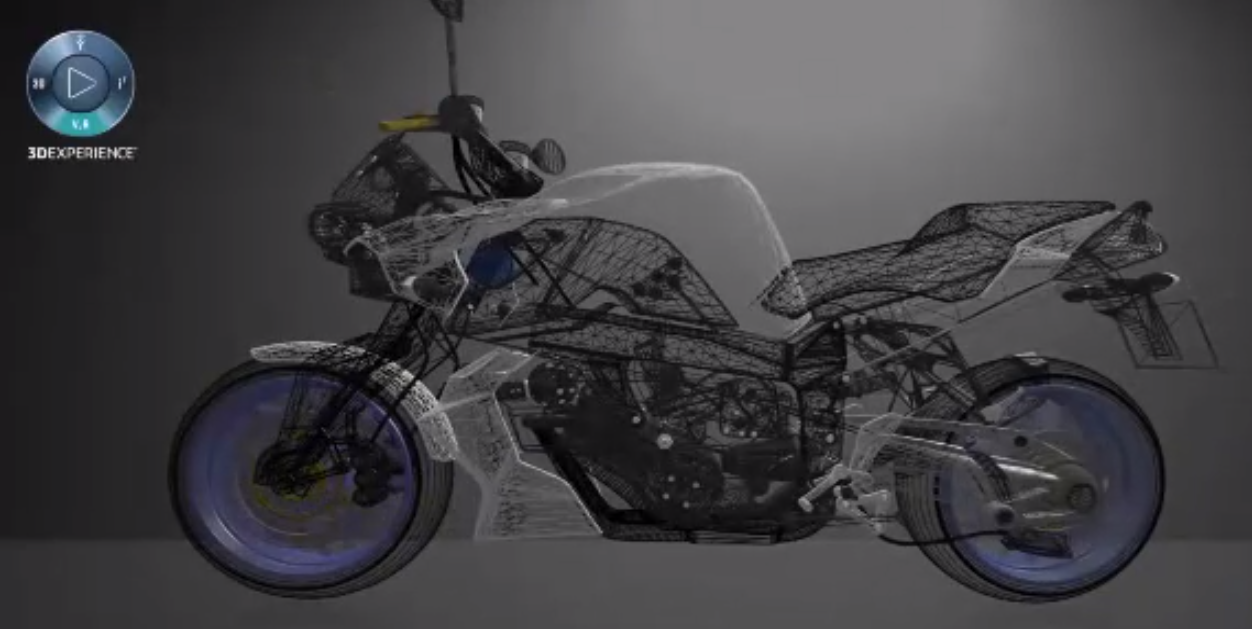
Efficient Optimization Based on FEW and CFD Simulations
Tosca – The Optimization Suite
The Tosca optimization suite provides fast and powerful structural and flow optimization solutions based on FEA and CFD simulations. Tosca optimization suite consists of two products: Tosca Structure is for optimized structural designs, and Tosca Fluid provides optimized fluid flow design concepts.
Tosca Structure delivers powerful optimization solutions for design of lightweight, stiff, and durable parts and assemblies within shorter development cycles to maximize performance, minimize material and weight, and discover new design possibilities. Tosca Structure offers functionalities for topology, shape, bead and sizing optimization.
Tosca Fluid enables topology optimization-driven design concepts for fluid flow systems and components. Use its capabilities to create innovative design ideas automatically for a defined flow task and available package space. Tosca Fluid’s unique technology helps you achieve the highest flow performance, quality and eco-efficiency.
Tosca Structure
Optimize with ABAQUS, ANSYS or MSC NSTRAN
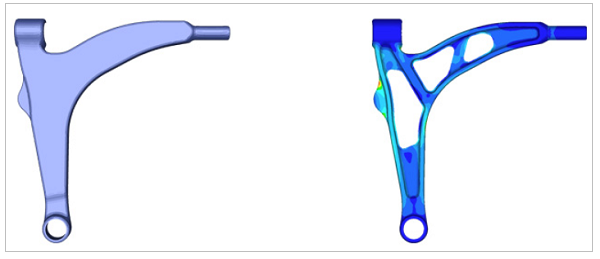
Tosca Structure is the market leading technology for structural optimization based on industry standard FEA packages (Abaqus, ANSYS, MSC Nastran) to create innovative and sustainable designs. From early conceptual design through to detailed design improvements Tosca Structure offers the full range of optimization solutions:
Key Benefits
- Economic use of existing IT investments
- Faster turnaround from analysis to design or manufacturing
- Less prototypes or right the first time
- Accelerated product development for a shorter time-to-market
- More durable and lightweight designs
- Optimized products drive innovations in your market
Optimization Modules
- Tosca Structure.topology
- Tosca Structure.sizing
- Tosca Structure.shape
- Tosca Sturcture.bead
Graphical User Interfaces
- Optimization module in Abaqus/CAE
- Tosca ANSA™ environment (TAe)
- Tosca Extension for ANSYS Workbench
- ANSA
- Tosca Structure GUI
For more information, download the Tosca structure brochure here.
Tosca Fluid
Design Concepts and CFD Optimization for Fluid Flow
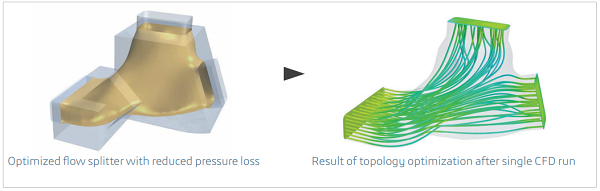
Tosca Fluid features unique design and non-parametric fluid flow topology optimization technology for components and systems. Utilize full design flexibility and create an innovative, optimized design concept for defined design spaces and flow tasks. No initial design is necessary. Only one solver run is needed using industry-standard CFD solvers.
Benefits of Tosca Fluid
- Economic use of existing IT investments
- Automated design development leads to less physical testing and a reduction in the number of prototypes
- Shorter development cycles by combining design and optimization of fluid flow tasks early in the design process
- Advanced designs with higher product performance and reduced energy consumption
- Faster time-to-market for innovative designs
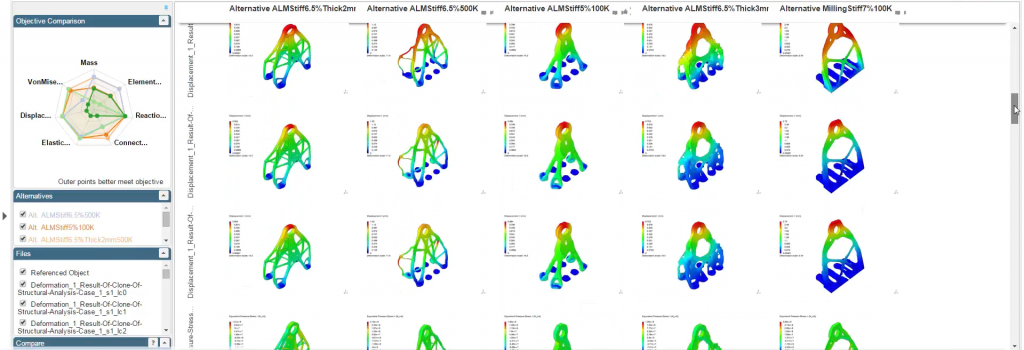
In today’s complex product development and manufacturing environment, designers and engineers are using a wide range of software tools to design and simulate their products. Often, chained simulation process flows are required in which the parameters and results from one software package are needed as inputs to another package and the manual process of entering the required data can reduce efficiency, slow product development, and introduce errors in modeling and simulation assumptions.
SIMULIA provides market-leading solutions that improve the process of leveraging the power of various software packages. Isight is used to combine multiple cross-disciplinary models and applications together in a simulation process flow, automate their execution across distributed compute resources, explore the resulting design space, and identify the optimal design parameters subject to required constraints.
Our proven simulation automation and optimization solutions enable engineering teams to:
- Drastically reduce design cycle time by integrating workflow processes in an automated environment.
- Deliver more reliable, better-quality products through accelerated evaluation of design alternatives.
- Lower hardware investments through effective use of legacy systems and more efficient job distribution.
- Eliminate the bottlenecks of ineffective communication by enabling secure design collaboration among partners.
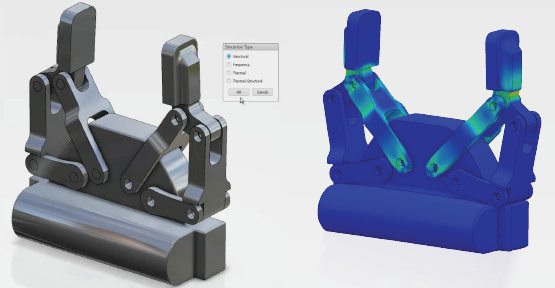
An intuitive Design Simulation solution for Designers looking for efficient product performance assessment under linear static conditions to guide the design process.
Description
Structural Designer provides intuitive design simulation-based guidance during product design process to easily get the technical insights needed for informed design decisions.
Structural Designer is a role developed with designers in mind. Design process is made of multiple iterations, multiple ‘what If’ ideas to successfully deliver the right product to manufacturing. With Structural Designer, any designer can assess product behavior for each design iteration to improve product performance and reduce time and cost of product development process.
Structural Designer delivers linear static, natural frequency, buckling and steady-state thermal simulation capabilities for fast and efficient product testing experience.
Benefits
- Structural Designer users can experience product performance virtually so that they can make better-informed design decisions.
- Better design decisions based on more complete information about product performance lead to better designs and better products
- The capability to assess product behavior early in the product development process enables companies in reducing potential late issues, reducing costs and developing innovative product.
- The simulation experience delivered by Structural Designer fits within the designer’s familiar design environment.
- Enables simulation of the physical behavior of parts and assemblies so that virtual testing can be conducted before physical prototypes are available for a faster product development process.
- The intuitive user experience makes simulation adoption possible for all designers.
- Users receive continuous guidance regarding where they are in the simulation process and what they need to do next, for easy adoption
- Sophisticated simulation technology is used automatically, while the options presented to the user are intuitive and explained in the language of product designers.
- Collaboration is built into the underlying 3DEXPERIENCE®.
- Data management, collaboration, and communities are all part of the global solution.
- Models built in Structural Designer can be shared directly with advanced simulation tools to enable the entire simulation team to collaborate with designers.
- Simulation Results can be easily reviewed by any project stakeholders in the 3DEXPERIENCE dashboard so they become insights for technical and business decision
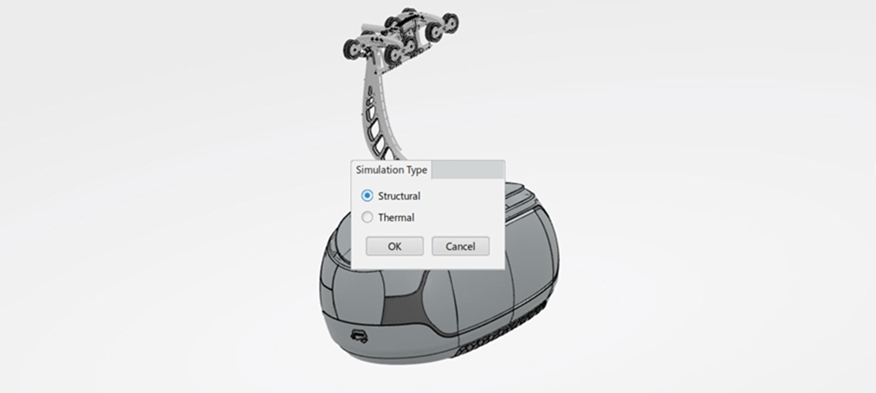
A comprehensive linear structural analysis solution to assess the performance of products during the product development process.
Description
Structural Engineer equips the Design Engineer with all the tools needed to efficiently conduct structural linear static, frequency, buckling, steady-state thermal simulation and modal dynamic response of product designs within 3DEXPERIENCE®. It provides unique capabilities to collaborate, simulate, and impact product development processes throughout the extended enterprise using state-of-the-art Abaqus simulation technology, ensuring accuracy of the virtual testing.
Benefits
- Easily assess large assembly performance with intuitive contact definition and powerful contact detection capability
- Evaluate structural KPIS of any geometry type with high quality meshing including solid, shell and beam elements with automatic mesh generation
- Enable high performance results visualization, particularly for very large models
- Include local compute up to 4 cores
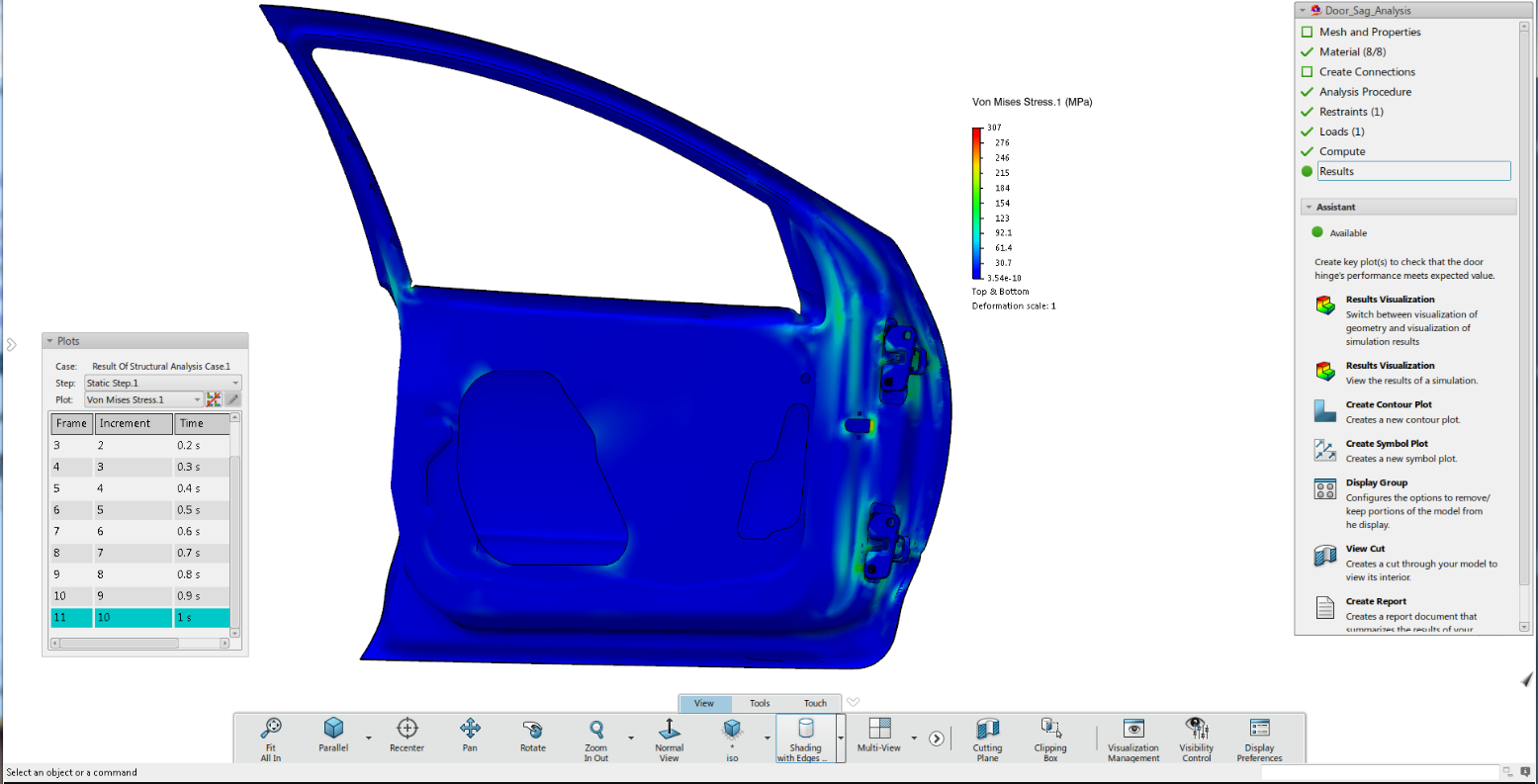
A Simulation Role for the Design Engineer who uses finite element techniques to assess the structural integrity of products subject to a wide range of loading conditions to guide design decisions for product performance and quality.
DESCRIPTION
Structural Analysis Engineer equips the Design Engineer with all the tools needed to conduct structural static, frequency, buckling, modal dynamic response, and structural thermal simulation of product designs within the 3DEXPERIENCE® platform. It provides unique capabilities to collaborate, simulate, and impact product development processes throughout the extended enterprise using state-of-the-art Abaqus simulation technology, ensuring accuracy of the virtual testing.
Benefits
- Provide Product Development, Mechanical, Design, and Simulation Engineers the powerful and intuitive tools needed to perform sophisticated structural simulations using best-in-class Abaqus simulation technology.
- Rather than being a domain for the Specialist only, Structural Analysis Engineer role provides a unique platform to leverage the value of simulation more widely throughout the engineering team
- The integration of Structural Analysis Engineer in the 3DEXPERIENCE Platform permits seamless design iteration based on simulation results.
- Delivers access to sophisticated simulation technology within an intuitive interface
- Provides high-quality, realistic results using the latest Abaqus technology coupled with the power of the 3DEXPERIENCE Platform
- More time efficient looking for geometry, part or assembly information, fastener data, etc. thanks to the collaborative nature of 3DEXPERIENCE.
- Simulation is managed as a core value of the 3DEXPERIENCE Platform allowing simulation IP to become a true corporate asset, unlike existing standalone Specialist tools
- Offers multistep structural scenarios for product performance and quality testing during the product design process
- Determine the strength of a product designed by reporting stress and deformations distribution
- Improve designs at risk for resonance and other dynamic effects
- Combine nonlinear base state with dynamic response for improved vibration prediction
- Predict temperature distribution within a design as well as thermal stress, which is due to steady-state or transient thermal loading
- Enables high performance results visualization, particularly for very large models
- Interrogation of realistic simulation results with speed, clarity, and control on the desktop for enhanced decision making.
- High performance visualization tools enable efficient post-processing of large-scale simulation data including an option to use remote machines for rendering and visualization computation.
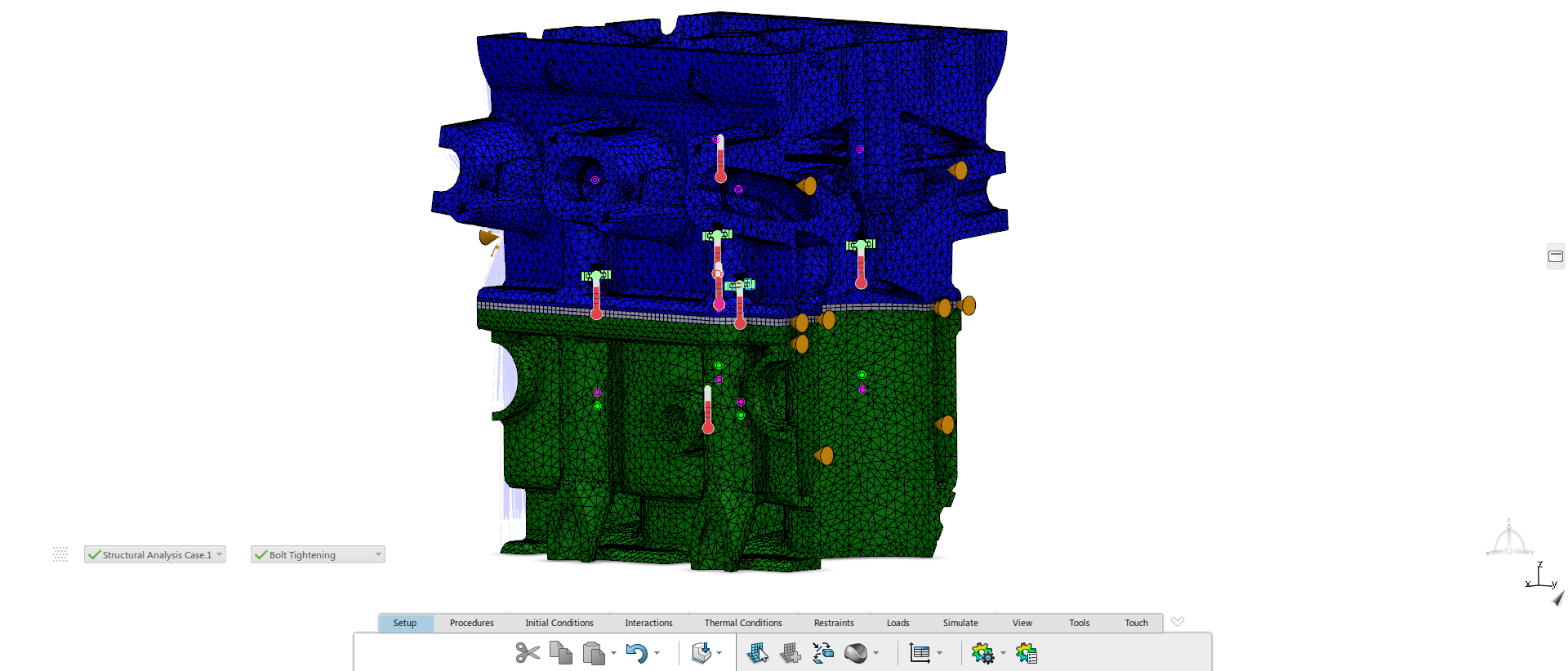
A Simulation Role for the Analyst that uses advanced finite element simulation techniques to understand and validate complex engineering problems
DESCRIPTION
Mechanical Analyst delivers proven world-class Abaqus realistic simulation technology in a seamless, intuitive experience. The toolset provides advanced capability from meshing, model management, visualization, and report generation, all within a fully immersive, intuitive, and modern user interface within the 3DEXPERIENCE® platform.
The Mechanical Analyst uses advanced finite element simulation techniques to understand and validate complex engineering problems. With extensive toolset to enhance productivity and efficiency, the Mechanical Analyst is equipped to conduct structural static, dynamic, and thermal simulation of product designs and assemblies within the 3DEXPERIENCE platform. Fully integrated with both the environment and with the geometry, Mechanical Analyst provides a unique platform to collaborate, simulate, and impact design processes throughout the extended enterprise using state-of-the-art Abaqus simulation technology. On the 3DEXPERIENCE platform, users can easily share models, techniques, methods, meshing and interconnection rules, materials, results, and all other simulation data with their colleagues and other stakeholders throughout the enterprise.
Benefits
- Provide Product Development and Mechanical Engineers the expert tools needed to perform advanced simulations using best-in-class Abaqus simulation technology
- Provides a unique platform to leverage the value of simulation more widely throughout the enterprise
- Less time spent looking for geometry, part assembly information, fastener data, etc. thanks to the collaborative nature of 3DEXPERIENCE
- Simulation is managed as a core value of the 3DEXPERIENCE Platform allowing simulation IP to become a true corporate asset, unlike existing standalone Specialist tools
- Improve designs at risk for resonance and other dynamic effects
- Linear load cases and multiple analysis cases for analyzing the response to a wide range of loading conditions
- Combine nonlinear base state with dynamic response for improved vibration prediction
- Fully dynamic transient time simulation within the 3DEXPERIENCE platform
- Workflows such a Drop, Crush, Forming, Shake, and Impact in all industries can be simulated
- High performance results visualization, particularly for very large models
- Enables interrogation of realistic simulation results with speed, clarity, and control on the desktop for enhanced decision making.
- High performance visualization tools enable efficient post-processing of large-scale simulation data including an option to use remote machines for rendering and visualization computation
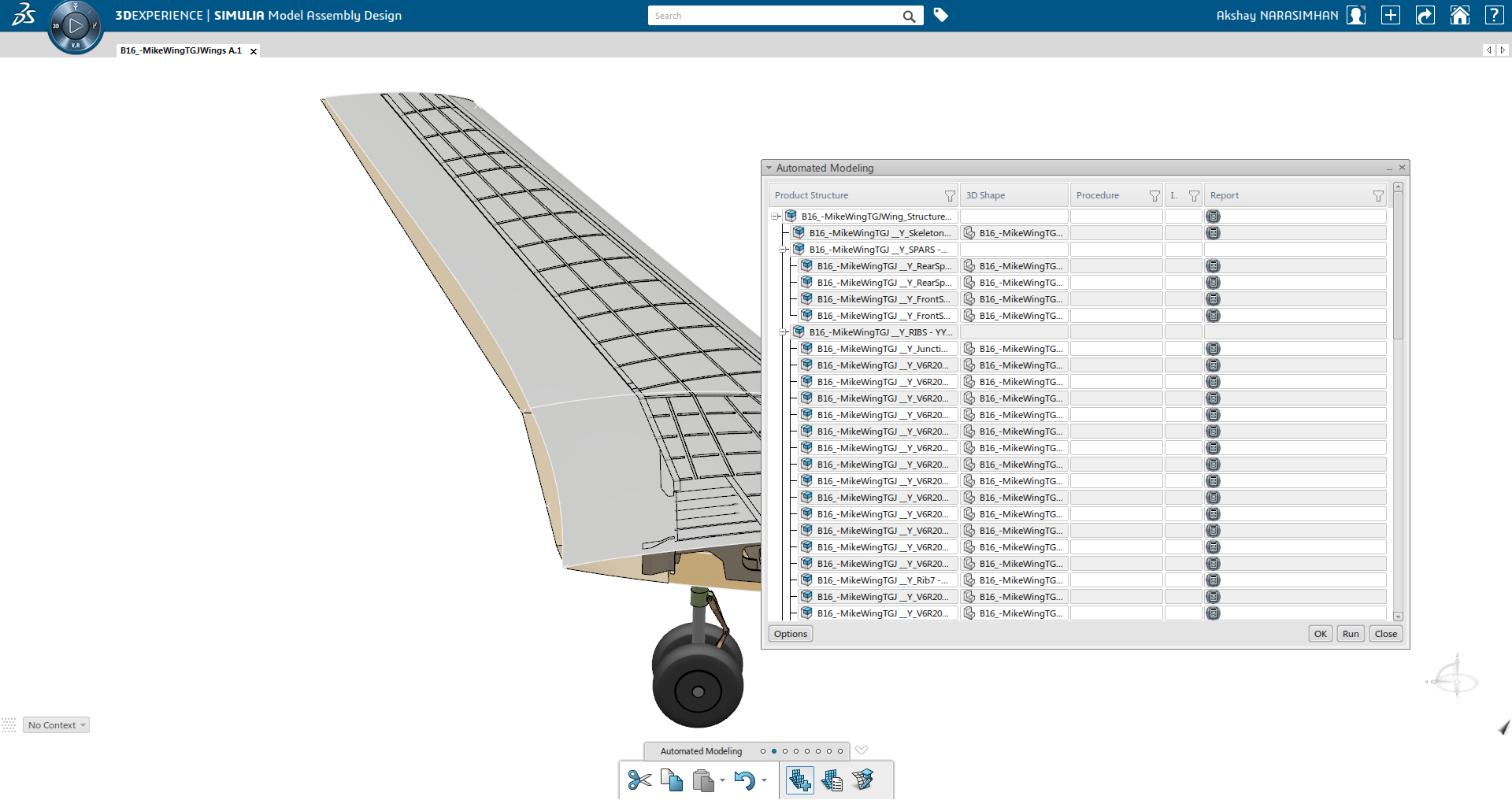
A Simulation Role for Analysts who specialize in the creation and/or management of large and complex finite element assemblies requiring automated modeling techniques and the collaborative efforts of several engineering teams.
DESCRIPTION
Assembly Modeling Specialist specializes in the creation and/or management of large and complex finite element assemblies requiring automated modeling techniques and the collaborative efforts of several engineering teams. The toolset enables the user to easily create Finite Element models for small or large assemblies, or import them from 3rd party tools, and manage them on the 3DEXPERIENCE® Platform.
Benefits
- Collaborative preparation of large-scale, multi-level assemblies leveraging multiple teams and locations
- Full traceability of the simulation model is ensured by the 3DEXPERIENCE Platform
- Automatic generation of simulation models via ‘fire and forget’ execution on HPC
- Less time spent looking for geometry, part assembly information, fastener data, etc. thanks to the collaborative nature of 3DEXPERIENCE.
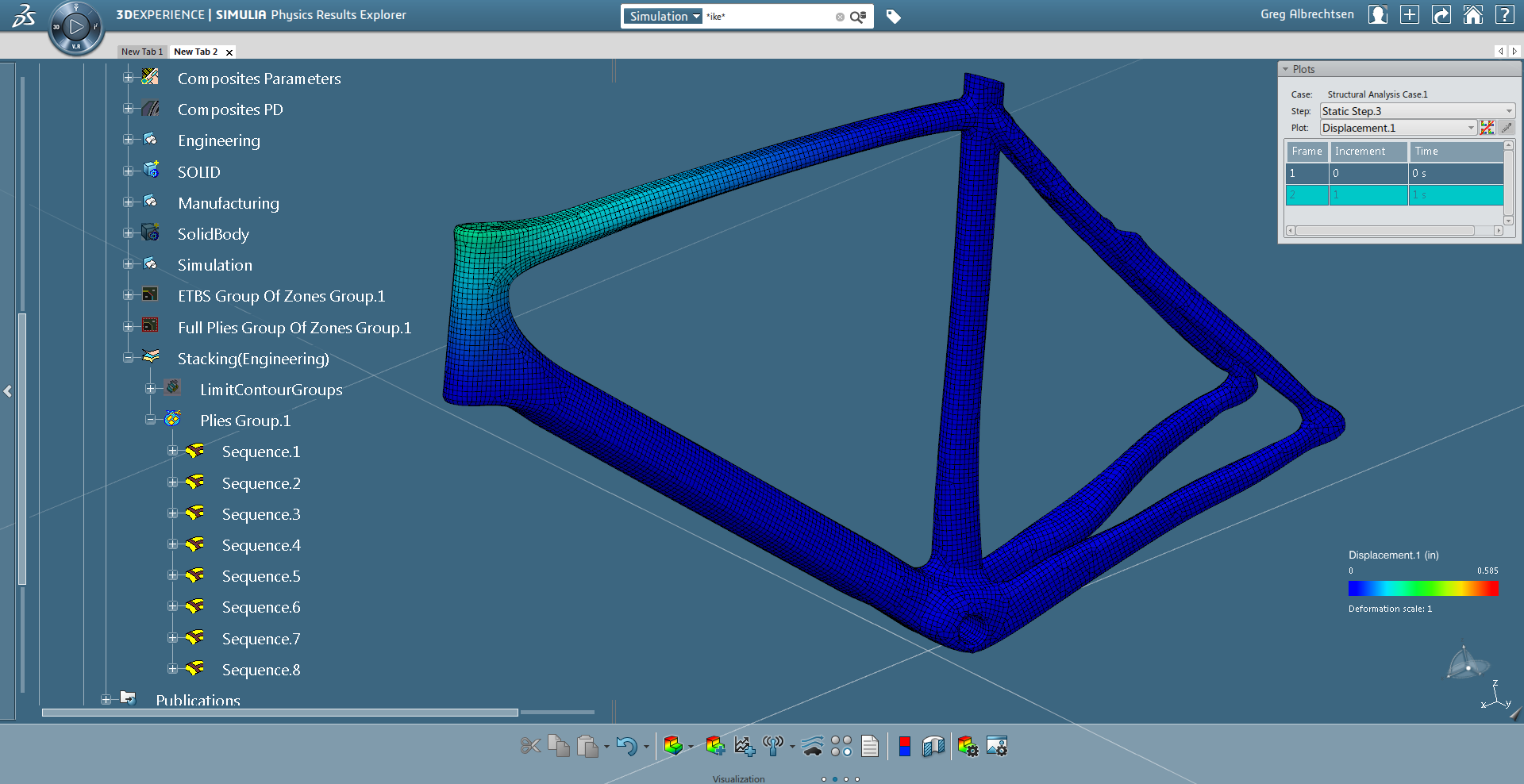
A Simulation Extension Role for Analysts who validate the structural integrity of products made of composite materials by directly reusing composite properties defined by the designer
DESCRIPTION
Composite Simulation Engineer allows to easily reuse composite layups defined with CATIA Composite Design tool in advanced simulations. Fully integrated with both the Simulation environment and the Composite parts Design & Manufacturing tools of the 3DEXPERIENCE® Platform, Composite Simulation Engineer extends the SIMULIA V+R Physics Apps to deliver a unique solution enabling users to collaborate, simulate, and impact composite design processes from preliminary design to validation runs.
Benefits
- Seamless integration with CATIA Composite tools
- Associativity with design allows quick iterations on the composite layup during the Preliminary Design stage (grid-based design, virtual stacking)
- Dedicated tools allowing composite simulation experts to run complex non-linear simulations within the fully immersive, intuitive, 3DEXPERIENCE Platform.
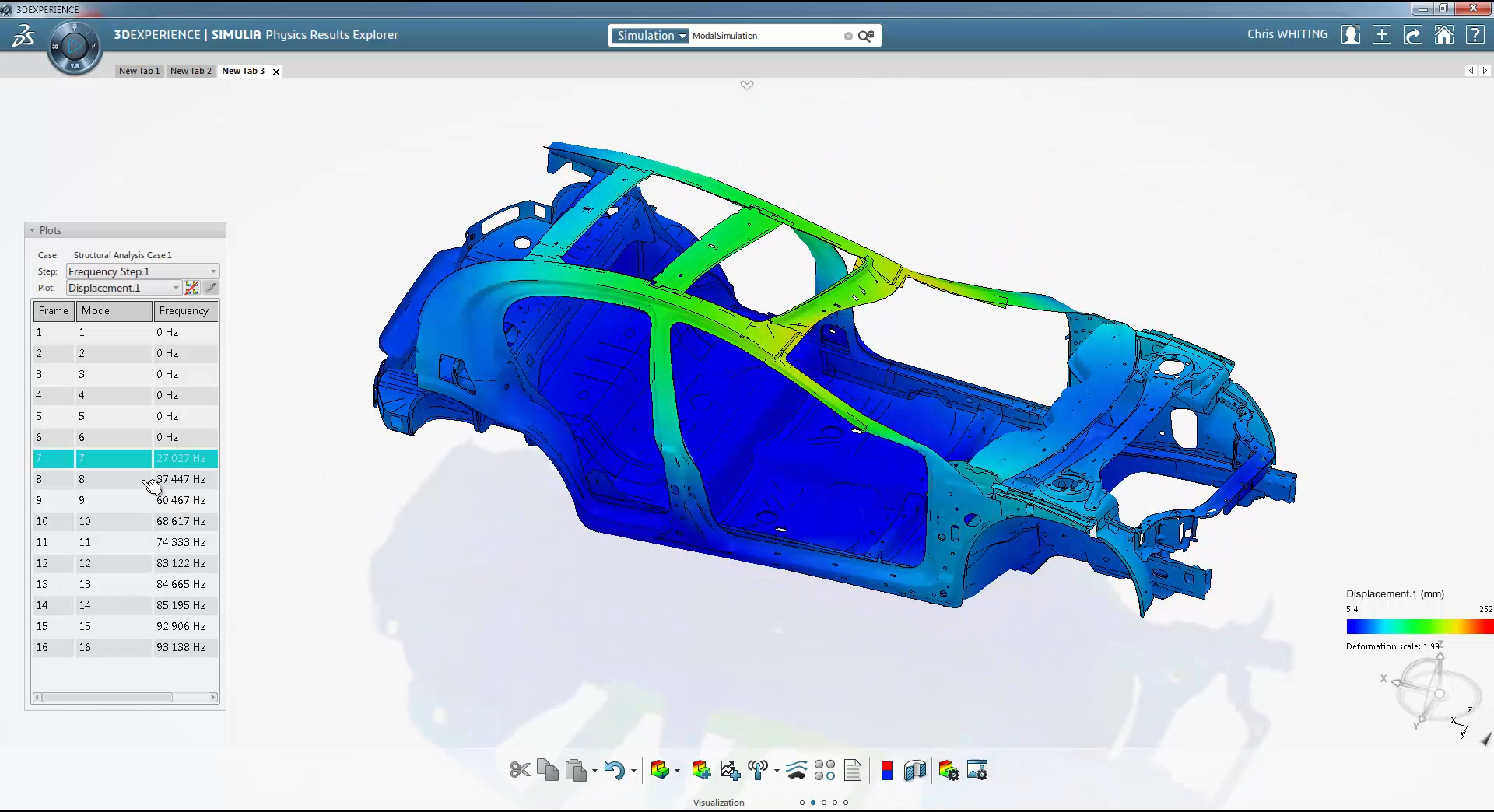
A Simulation Role for the Analyst that uses advanced linear static and linear dynamic simulation techniques to validate the engineering requirements of complex products subject to dynamic loading scenarios.
DESCRIPTION
Structural Vibration Analyst uses advanced linear static and linear dynamic simulation techniques to validate the engineering requirements of complex products subject to dynamic loading scenarios. The toolset – specifically designed to appeal to users in the Transportation & Mobility and Aerospace & Defense industries – provides a simulation environment to perform static perturbation, frequency extraction and linear dynamics response analysis of structures. It is based on state-of-the-art features and capabilities of the Abaqus solver and provides high performance solutions.
BENEFITS
Simulation results from the best-in-class Abaqus solver
- Understand the vibration response of structures subject to dynamic loading in time or frequency domain
- Analyze several linear dynamics scenarios including static perturbation, natural frequencies, harmonic response and modal transiental dynamics
- Consider advanced damping treatment
Support for the NASTRAN solver is available
Generative Modeling Environment
- Automatically generate meshes or leverage interactive toolset to create high quality models
- Reuse design intent and enhance existing design features with simulation behaviors such as connections, materials, section properties etc.
- Associative modeling enables users to rapidly study design iterations as the product progresses through the design cycle
State-of-the-Art Visualization
- Visualization of massive simulation models with superior performance and speed
- High quality rendering capability with flexible toolsets to control
Collaborate and Communicate Ideas
- Collaborate and share simulation results with key stakeholders to guide design decisions
- Exchange live data across groups and organizations through common data management and data structures allowing designers to work directly with simulation specialists improving productivity
A Simulation Role for the Analyst that uses advanced linear static and dynamic simulation techniques to validate the engineering requirements of complex products that include acoustic enclosures subject to dynamic loading scenarios
DESCRIPTION
Noise & Vibration Analyst uses advanced linear static and dynamic simulation techniques to validate the engineering requirements of complex products that may include acoustic enclosures subject to dynamic loading scenarios. The toolset – specifically designed to appeal to users in the Transportation & Mobility and Aerospace & Defense industries – provides a comprehensive simulation environment for performing accurate noise and vibration analysis to improve product performance and enhance the consumer experience. It is based on state-of-the-art features and capabilities of the Abaqus solver which provide high-performance solutions.
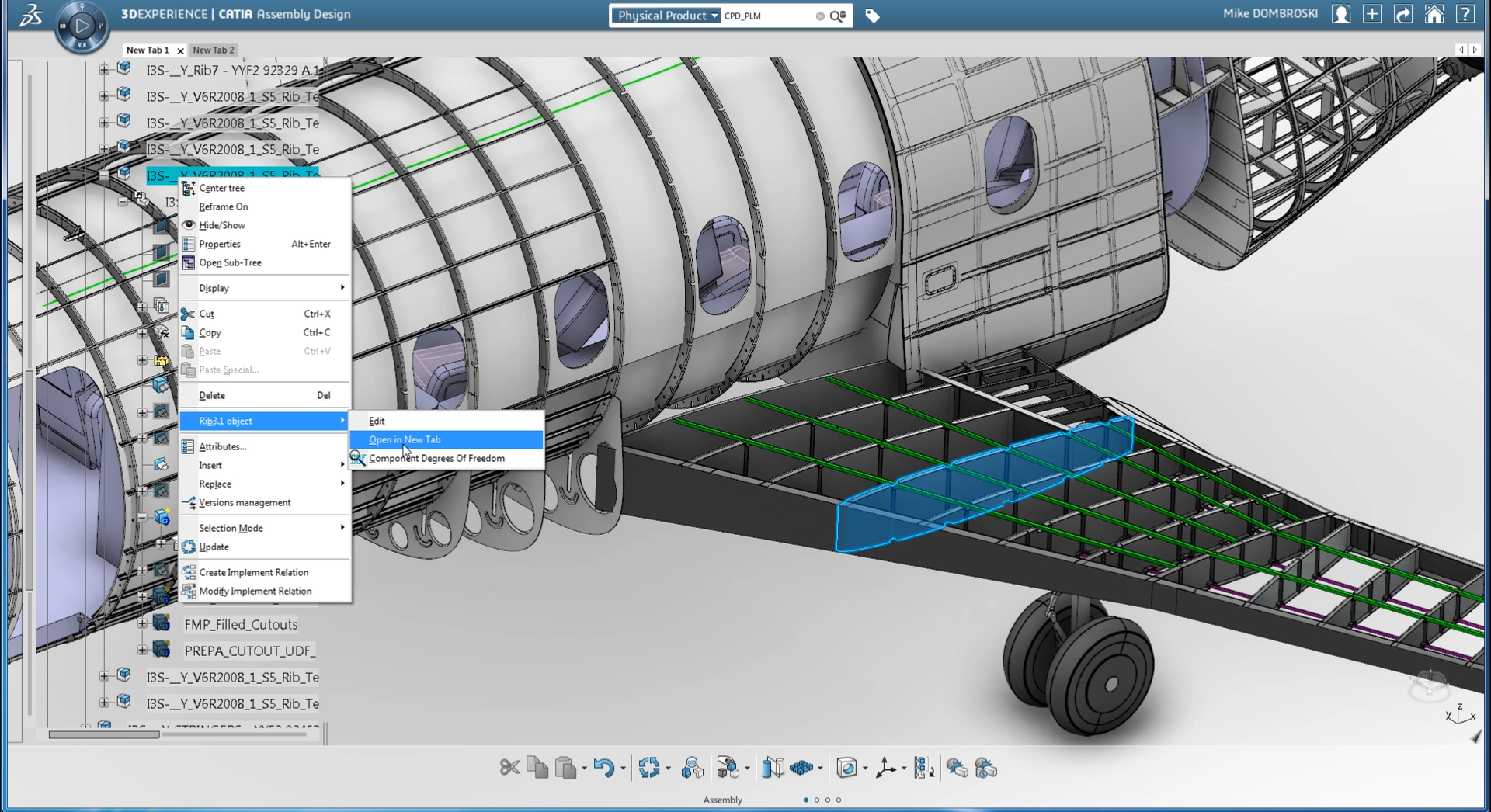
A Simulation Extension Role for Analysts who create geometry for simulations using parametric or direct modeling techniques.
DESCRIPTION
Simulation Geometry Modeler Extension Role adds capability a base role to enable users who have no access to CATIA geometrical modeler to get the minimum set of tools allowing the creation of simple geometries, surfaces and solids, using the best, market-proven, CAD modeler in the world.
Benefits
- Feature-based, parametric modeling tools allowing quick iterations between Design and Simulation
- New Direct Modeling tools enabling simulation specialists to rapidly create, modify or repair geometries without requiring any CAD expertise
- Full compatibility with the other tools of the 3DEXPERIENCE® Platform
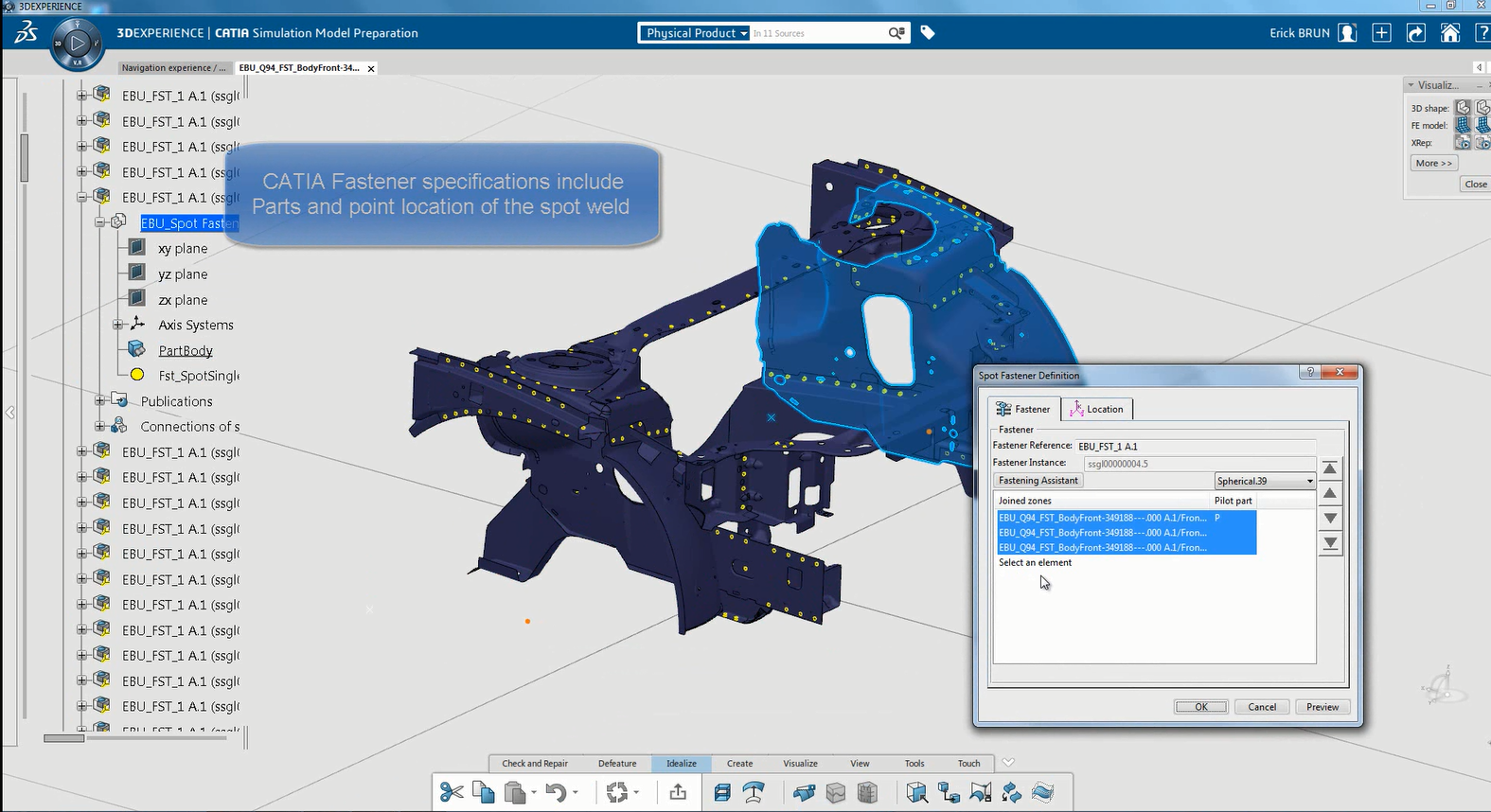
A Simulation Role for Analysts who specialize in the creation and/or management of large and complex finite element assemblies requiring automated modeling techniques and the collaborative efforts of several engineering teams
DESCRIPTION
Finite Element Modeling and Assembly Specialist specializes in the creation and/or management of large and complex finite element assemblies requiring automated modeling techniques and the collaborative efforts of several engineering teams.
The toolset enables the user to easily create Finite Element models for small or large assemblies, or import them from 3rd party tools, and manage them on the 3DEXPERIENCE® Platform. Finite Element model representations can be created based on predefined rules, including geometry idealization, high quality meshing and creation of sections and other abstractions (masses…). The meshes can be checked and edited using state-of-the-art meshing tools and then the model itself can be checked and assembled using a wide variety of predefined connections.
Finite Element Modeling Specialist allows Specialist users to define procedures through a scripting language, thus capturing the company’s modeling standards and best-practices, which can be shared with other users across the enterprise on the 3DEXPERIENCE Platform.
Benefits:
- Collaborative tool to build large-scale, multi-level assemblies leveraging multiple teams and locations
- Provide Product Development, Mechanical, Design, and Simulation Engineers the expert tools needed to prepare advanced simulations.
- Automatic generation of high quality simulation models via ‘fire and forget’ execution on HPC
- Less time spent looking for geometry, part assembly information, fastener data, etc. thanks to the collaborative nature of 3DEXPERIENCE.
Providing a solution for Engineers who assess plastic parts for manufacturability with filling and packing simulation.
DESCRIPTION
Plastic Injection Analysis Engineer provides the part and mold designers with the ability to explore and compare mold design and manufacturing alternatives by simulating the injection molding process itself as part of the evaluation of the mold design. This allows users to accelerate the design process by reducing trial-and-error iterations and create improved mold designs that deliver better-performing molded parts, including consideration of manufacturing constraints.
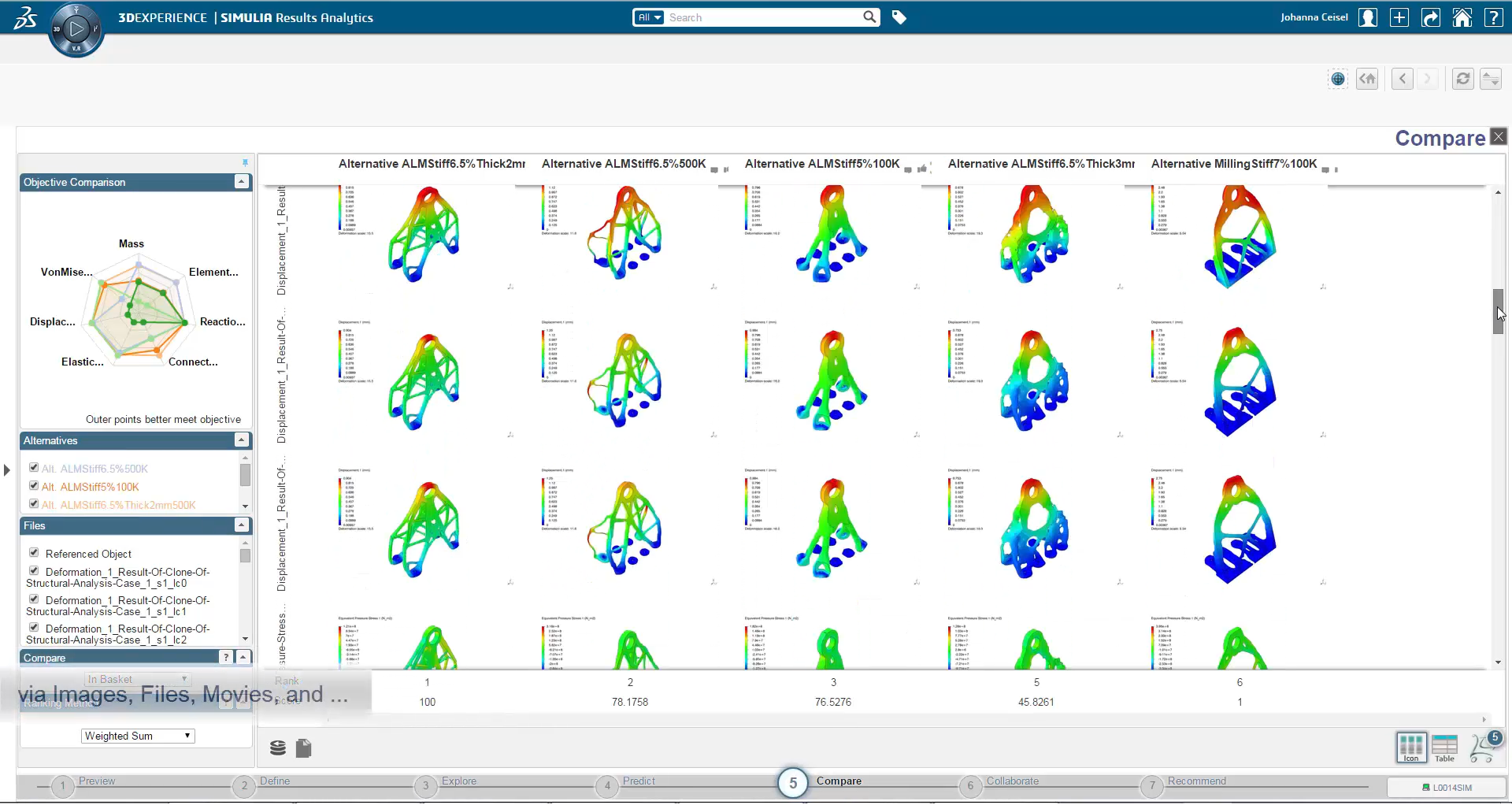
Rapidly transform large data into verifiable decisions with advanced analytics
DESCRIPTION
Results Data Analyst role provides dedicated functionality for data post-processing and collaborative decision support. By leveraging advanced analytics, users can rapidly transform data to verifiable decisions. Virtual and physical testing, by its very nature, generates large amount of data and requires analytics tools to extract its value through post-processing, visualization, and trade-off analysis. Through Results Data Analyst role users can now unlock their data to collaboratively answer common questions, such as “What if?” or “What is my best option?” while retaining decision history and reference material in one place.
Users can easily access and merge data sets, refine data by applying filtering, obtain immediate insights through a customizable ranking engine, and predict better outcomes using predictive analytics. They can then compare alternatives in 3D, leveraging lightweight viewers. Users can also collaborate with decision makers via discussion threads and preference trades to explicitly and transparently evaluate scenarios and verify requirements.
Benefits
- Easier Data Access and Preparation
- Read any PLM Object
- Automatic Data Merge of multiple data sources based on simulation logic
- Eliminate timely movement of large data and models
- Uncover Hidden Patterns in Simulation Results Data
- Use analytics and advanced visualizations to uncover new and emerging patterns in the data of post-processed simulations
- Faster, Interactive 3D Visualization
- Data Compression via Analytics
- Server Rendering and Binning
- Embedded 3D Lightweight Viewers
- Generate Predictive Insights
- Leverage data investment by generating mathematical models for predictive insights using advanced analytic methods
- Share and manage predictions via traceable approximation objects, FMUs, or co-efficient file for further design exploration.
- Fact Based Decisions
- Rigorously assess large set of alternatives against requirements via ordinal ranking engine using Multi-Criteria Decision Making Techniques
- Improve Decisions through Collective Intelligence
- Collaboratively compare alternatives and validate against requirements with stakeholders from anywhere via web application on premise or cloud (FD04)
- Decision Traceability
- Retain “the why” of a decision with decision history, discussion threads, and reference material in one place
- Save and share analysis and decisions with stakeholders via “live report”
- Tie decisions to designs, project tasks, requirements, and engineering change requests
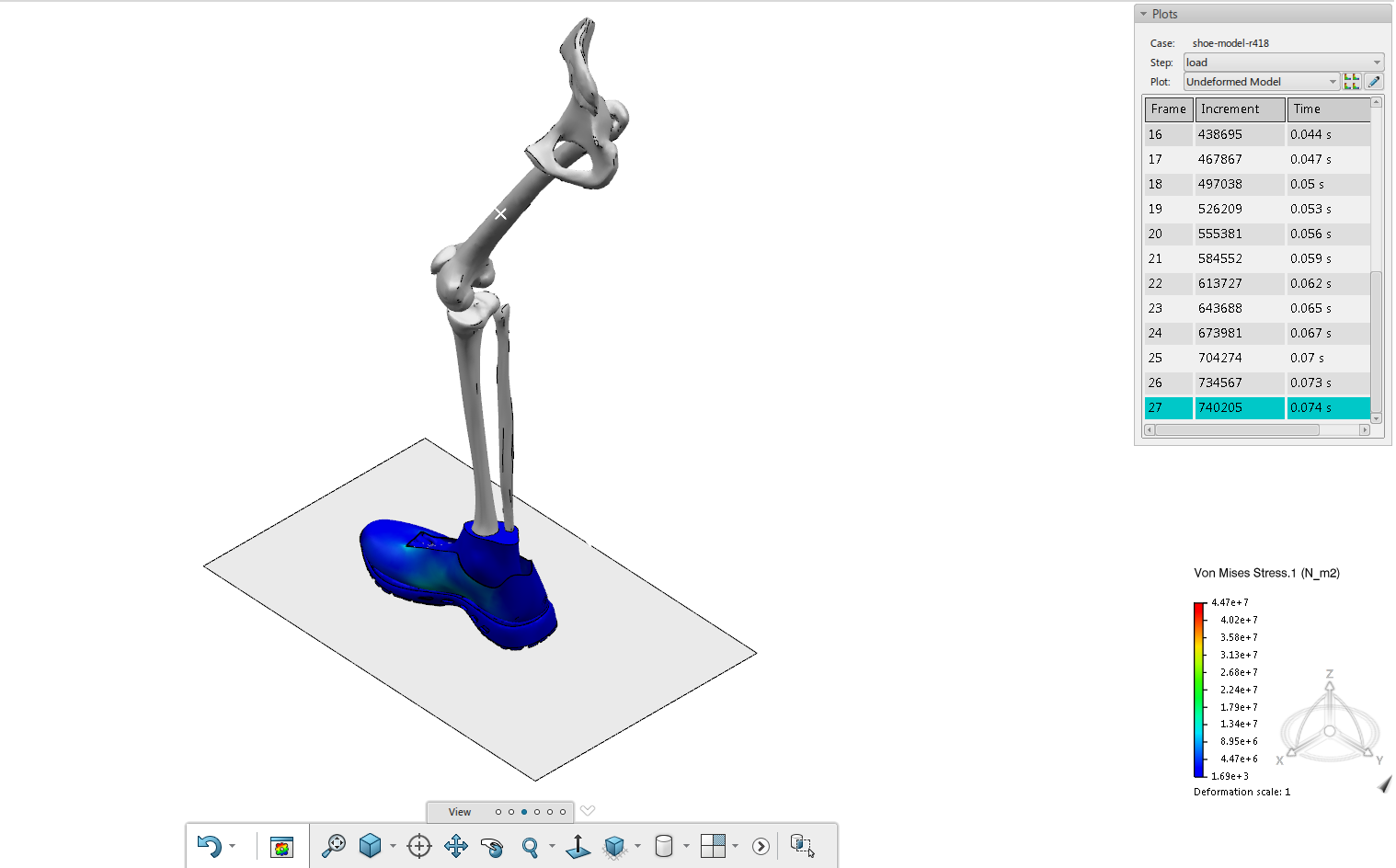
A Simulation Role for Analysts who use advanced finite element simulation techniques and need a high-performance tool for efficient results visualization of very large data sets.
DESCRIPTION
Simulation Results Analyst provides a new paradigm in results visualization. Results files are not copied to the user workstation and visualization computations are performed within the distributed environment. The result is a state-of-the-art visualization capability enabling the processing of very large models with breathtaking performance.
Benefits
- Provides results visualization for all physics simulations within the 3DEXPERIENCE® Platform.
- Allows post-processing and visualization of very large models with best-in-class rendering performance
- Support results visualization of imported simulations including Abaqus ODB and Nastran OP2 formats.
- Utilizes High Performance Computing (HPC) resources to perform results visualization rather than only the user’s workstation.
- Enables the generation of lightweight simulation results content for rapid visualization using 3DPlay app using 3DEXPERIENCE or tablet devices.
- Utilization of HPC resources to render large models resulting in state-of-the-art performancee
- File copy from compute server to local workstation for visualization is not performed
- Modern platform with clean, easier to learn, user interface.
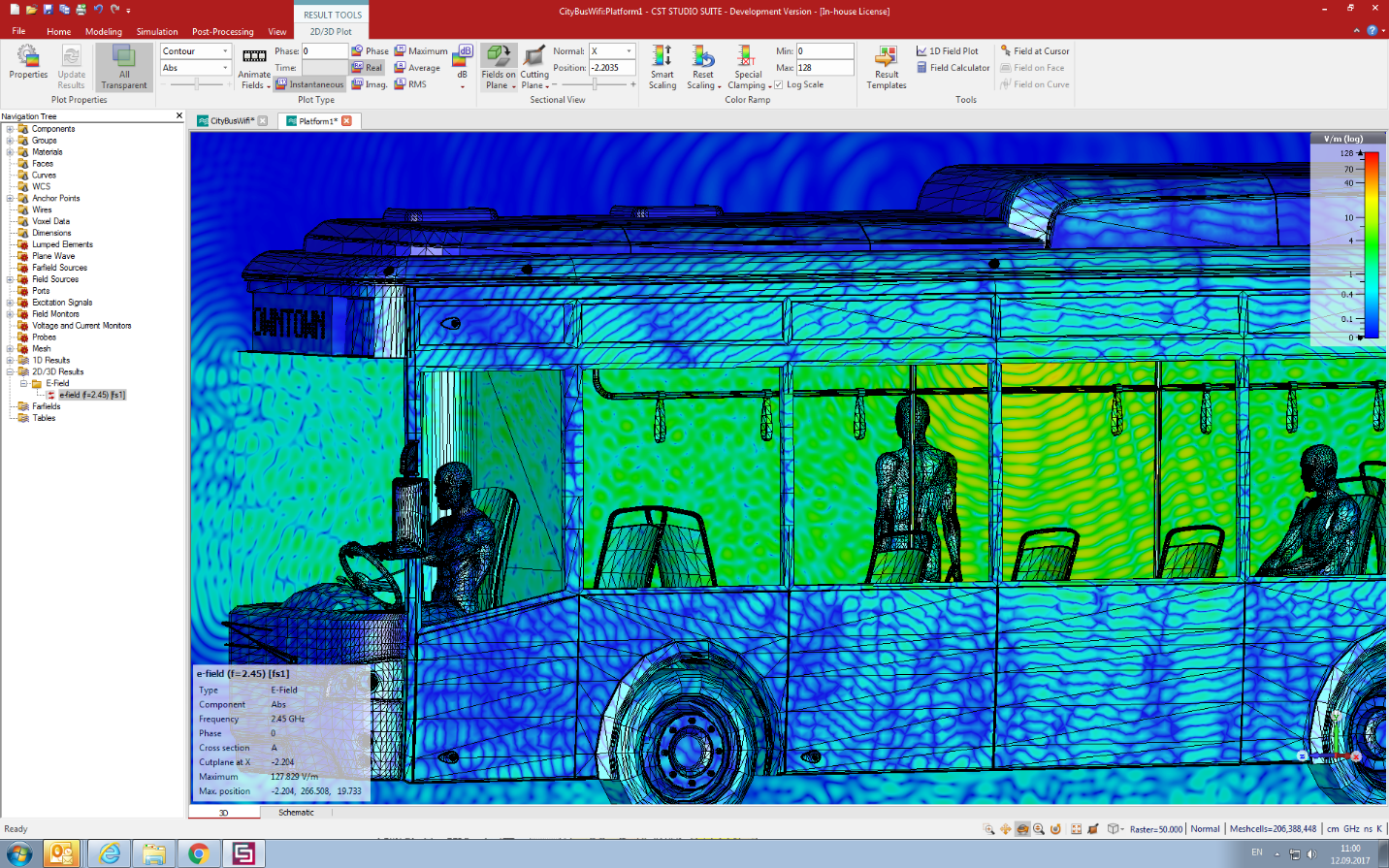
Electromagnetic field simulation software
CST Studio Suite is a high-performance 3D EM analysis software package for designing, analyzing and optimizing electromagnetic (EM) components and systems.
Electromagnetic field solvers for applications across the EM spectrum are contained within a single user interface in CST Studio Suite. The solvers can be coupled to perform hybrid simulations, giving engineers the flexibility to analyze whole systems made up of multiple components in an efficient and straightforward way. Co-design with other SIMULIA products allows EM simulation to be integrated into the design flow and drives the development process from the earliest stages.
Common subjects of EM analysis include the performance and efficiency of antennas and filters, electromagnetic compatibility and interference (EMC/EMI), exposure of the human body to EM fields, electro-mechanical effects in motors and generators, and thermal effects in high-power devices.
CST Studio Suite is used in leading technology and engineering companies around the world. It offers considerable product to market advantages, facilitating shorter development cycles and reduced costs. Simulation enables the use of virtual prototyping. Device performance can be optimized, potential compliance issues identified and mitigated early in the design process, the number of physical prototypes required can be reduced, and the risk of test failures and recalls minimized.
Fluid and CFD Simulation
SIMULIA’s Computational Fluid Dynamics (CFD) simulation offerings allow our customers to engineer products ensuring accurate real world performance predictions with fast turnaround speeds. SIMULIA’s Fluids technologies allow customers to solve a vast array of challenges spanning industries and application use cases.
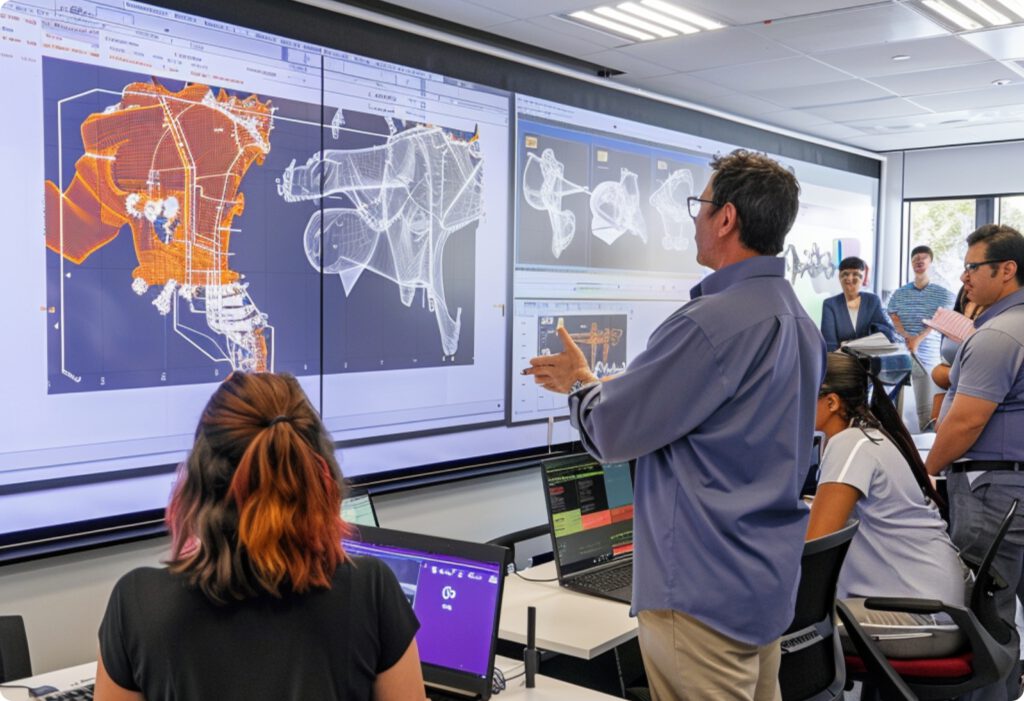
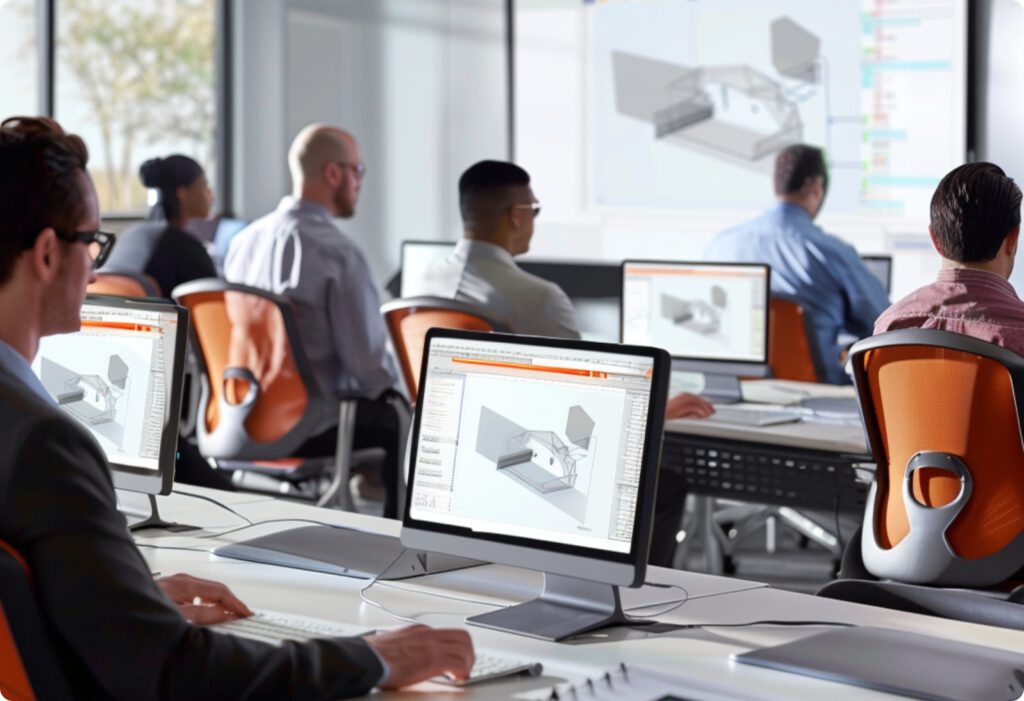
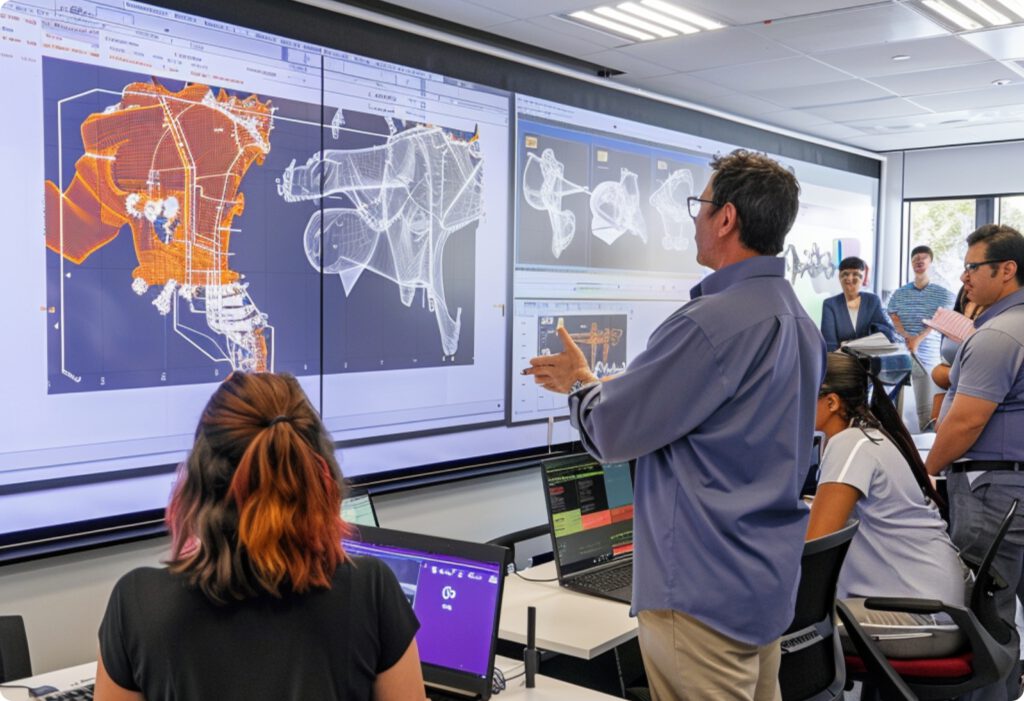
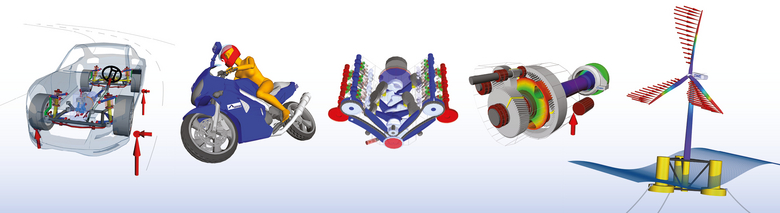
Simpack simulation software is particularly well-suited to high frequency transient analyses, even into the acoustic range. Simpack was primarily developed to handle complex non-linear models with flexible bodies and harsh shock contact.
From initial concept designs, through to production and redesigns, Simpack is used to help engineers fully comprehend and optimize systems, vastly reduce the need for physical prototyping, reduce time-to-market and improve product quality and lifespan. In essence Simpack enables manufacturers to gain a competitive edge by offering the ability create high quality products in a time and materially efficient manner thus reducing overall costs in design, production and maintenance.
Diversity and good connectivity to various multi-physics software (e.g. control, hydraulics and FEA) enable Simpack to be easily integrated into any manufacturer’s already-established development processes.
All Simpack features are 100% compatible. Therefore, new software developments for one particular engineering field benefit all Simpack users regardless of the application area.
As part of the SIMULIA Brand, Simpack is now the strategic MBS component of the Dassault Systèmes 3DEXPERIENCE® portfolio.