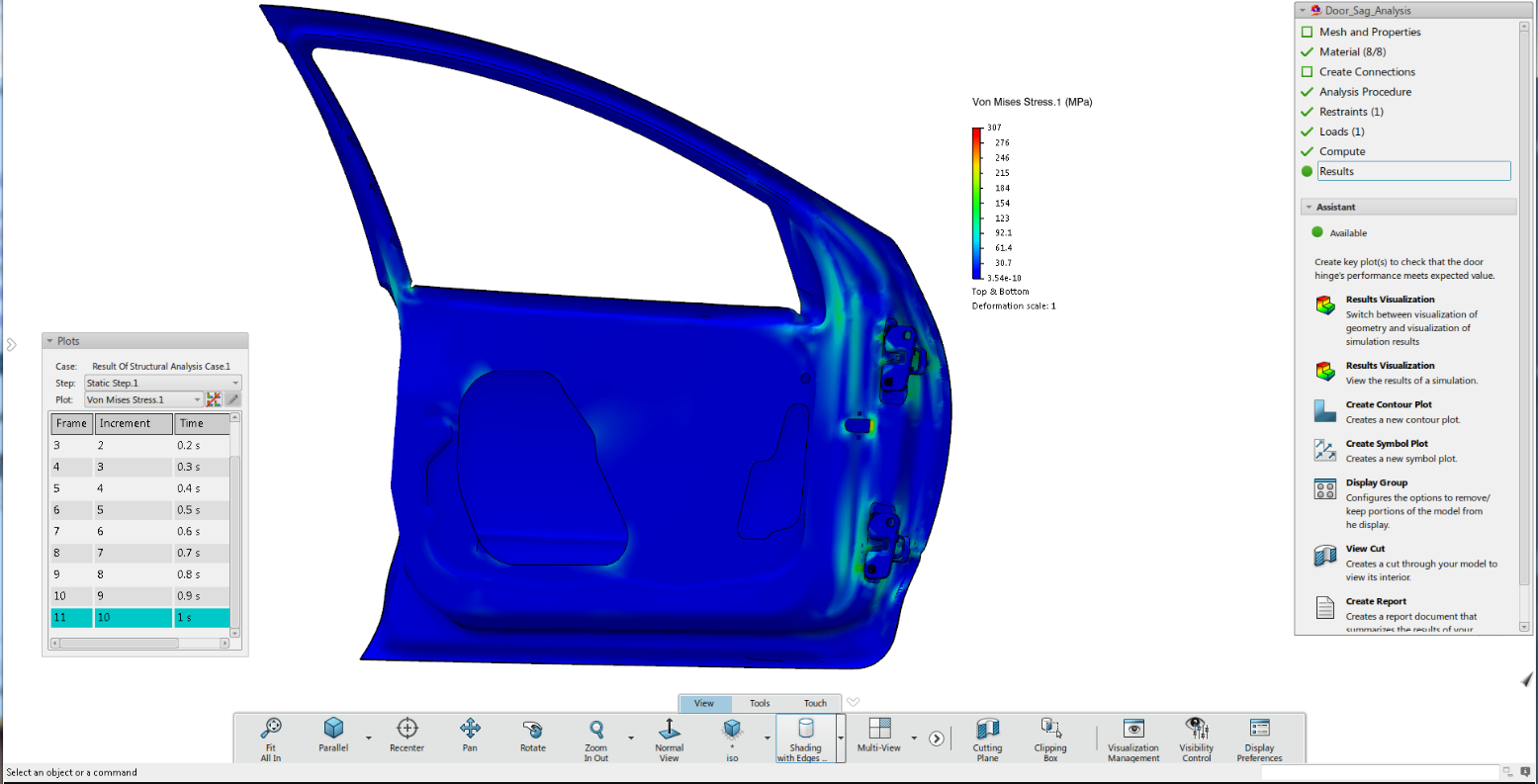
A Simulation Role for the Design Engineer who uses finite element techniques to assess the structural integrity of products subject to a wide range of loading conditions to guide design decisions for product performance and quality.
DESCRIPTION
Structural Analysis Engineer equips the Design Engineer with all the tools needed to conduct structural static, frequency, buckling, modal dynamic response, and structural thermal simulation of product designs within the 3DEXPERIENCE® platform. It provides unique capabilities to collaborate, simulate, and impact product development processes throughout the extended enterprise using state-of-the-art Abaqus simulation technology, ensuring accuracy of the virtual testing.
Benefits
- Provide Product Development, Mechanical, Design, and Simulation Engineers the powerful and intuitive tools needed to perform sophisticated structural simulations using best-in-class Abaqus simulation technology.
- Rather than being a domain for the Specialist only, Structural Analysis Engineer role provides a unique platform to leverage the value of simulation more widely throughout the engineering team
- The integration of Structural Analysis Engineer in the 3DEXPERIENCE Platform permits seamless design iteration based on simulation results.
- Delivers access to sophisticated simulation technology within an intuitive interface
- Provides high-quality, realistic results using the latest Abaqus technology coupled with the power of the 3DEXPERIENCE Platform
- More time efficient looking for geometry, part or assembly information, fastener data, etc. thanks to the collaborative nature of 3DEXPERIENCE.
- Simulation is managed as a core value of the 3DEXPERIENCE Platform allowing simulation IP to become a true corporate asset, unlike existing standalone Specialist tools
- Offers multistep structural scenarios for product performance and quality testing during the product design process
- Determine the strength of a product designed by reporting stress and deformations distribution
- Improve designs at risk for resonance and other dynamic effects
- Combine nonlinear base state with dynamic response for improved vibration prediction
- Predict temperature distribution within a design as well as thermal stress, which is due to steady-state or transient thermal loading
- Enables high performance results visualization, particularly for very large models
- Interrogation of realistic simulation results with speed, clarity, and control on the desktop for enhanced decision making.
- High performance visualization tools enable efficient post-processing of large-scale simulation data including an option to use remote machines for rendering and visualization computation.