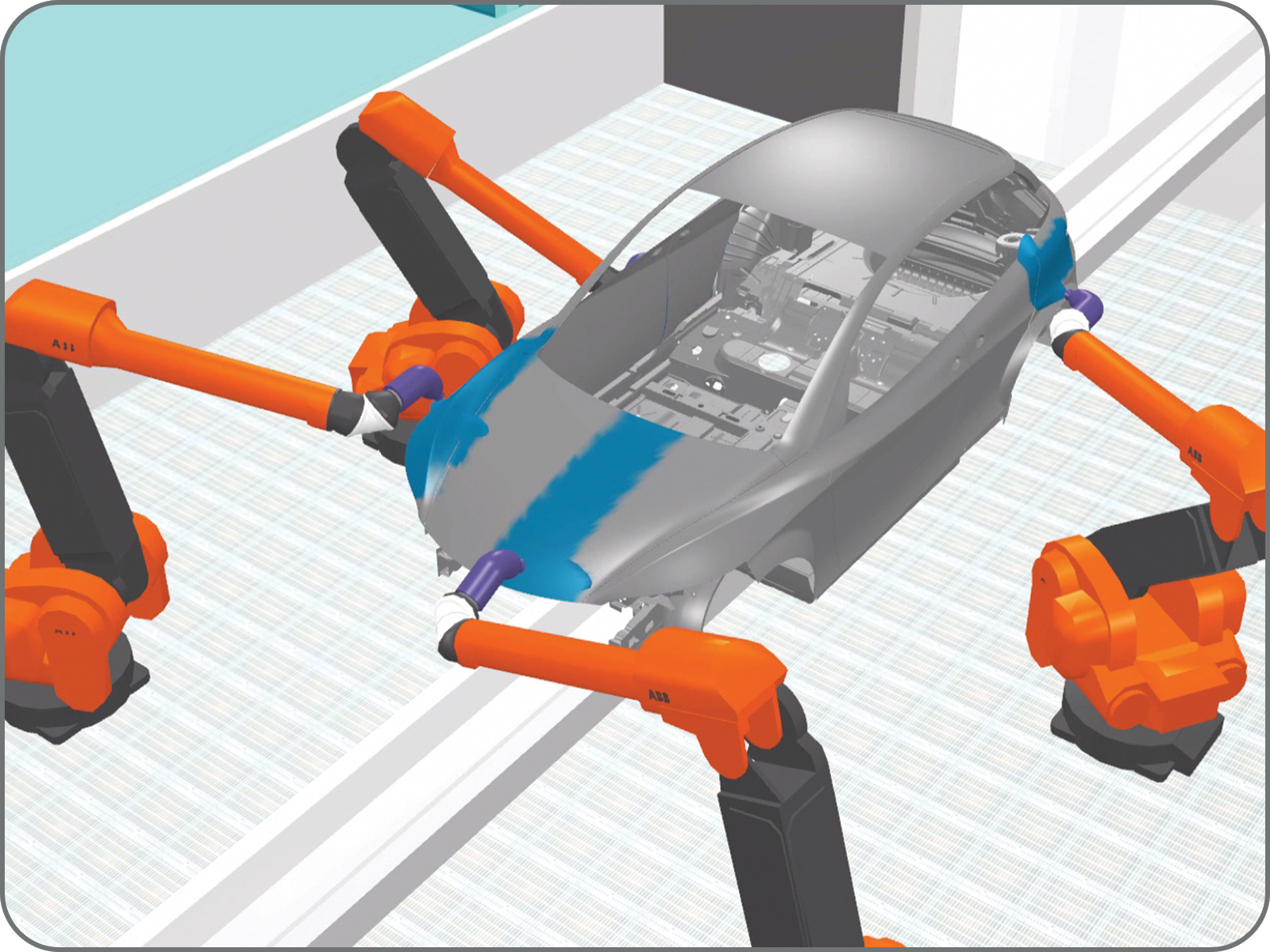
Description
DELMIA Robotics Surface Engineer (RSF) facilitates the creation and simulation of robotic surface processes—spraying, flaming, grinding, and finishing. In the integrated 3DEXPERIENCE® environment, Simulation Engineers use product geometry to validate robotic workcells and advanced robot processes in the immersive context of the 3D environment.Simulation Engineers can position resources, create robot trajectories, simulate robotic functions and create a complete workcell sequence. They can define, validate, and optimize surface processes and setups ahead of delivery to the shop floor. Users can draw from the DELMIA robot library of over 1500 robots. Line-tracking capabilities insure that the most accurate simulation is achieved.
Key Benefits
- Accurate surface based programming – RSF uses the surface representation of the 3D model to create robot trajectories. This gives the user an accurate path that follows the contour of the surface. The user can input the number of passs, the direction, and the overlap. This surface based robot trajectory is ideal for multiple robot applications such as painting, spray sealant, flaming, and others.
- Graphic representation of material deposition – RSF users can model the spray nozzle and pressure parameters of the spray gun. As the robot moves the gun across the surface, RSF graphically represents the thickness of the material deposited on the surface using different colors or on a graph. The granularity of each representation is determined by the user. This allows the user to produce highly accurate robot programs and reduces wasted materials.
- Robot Line Tracking – RSF performs line tracking for the user. When products are on moving conveyance systems, the robot needs to be able to track that motion in order to provide a quality finish. Automotive paint lines, for example, almost exclusively use moving conveyance systems. Robot line tracking ensures that the robot trajectory is followed with a high degree of accuracy, no matter where the conveyor is moving or how fast.
- Simulation that eliminates programming errors and rework – Powerful PLM simulation in the immersive environment gives programmers upfront validation of cell layout, tooling designs and advanced robot programs using product geometry in the factory context. They can simulate sequences in multi-robot cells to optimize productivity. RSF includes the Realistic Robot Simulation I (RRS-I) standard for increased trajectory and cycle-time accuracy. Reachability, analysis, collision detection and cycle-time analysis tools eliminate rework and programming errors.
- Fast, simple robotic workcell layout – RSF lets users choose from an extensive library of robot and controller models from all major industrial robot manufacturers. Auto placement and workspace envelope tools help users position the robot in a reachable position and benefit from early feasibility studies.
Early discovery and resolution of design for manufacturing (DFM) issues – RSF lets users perform robot task feasibility studies early in the planning and detailing stages, reducing the need for costly product changes.