With the Dassault Systèmes 3DEXPERIENCE® platform, the digital thread is extended to include the service and maintenance of products. The integrated platform allows service process engineers to begin planning service activities even before the design has been finalized.
The DELMIA Service Process Engineer role on the 3DEXPERIENCE platform enables users to define and visualize service and maintenance processes in 3D. It leverages up-to-date engineering data to build maintenance task activities and plan service resources. Easily create the Service Bill of Materials (BOM) and work instructions as well as capture and re-use maintenance practices across the enterprise.
Create Service Bill of Materials
With DELMIA Service Process Engineer, the Service BOM is created using the engineering data and enriched with service or maintenance specific attributes. Parts that should be serviced together can be grouped together as a Service Kit, independent from the Engineering BOM or Manufacturing BOM. Thanks to the 3DEXPERIENCE platform, the Service Bill of Materials is managed with up-to-date data.
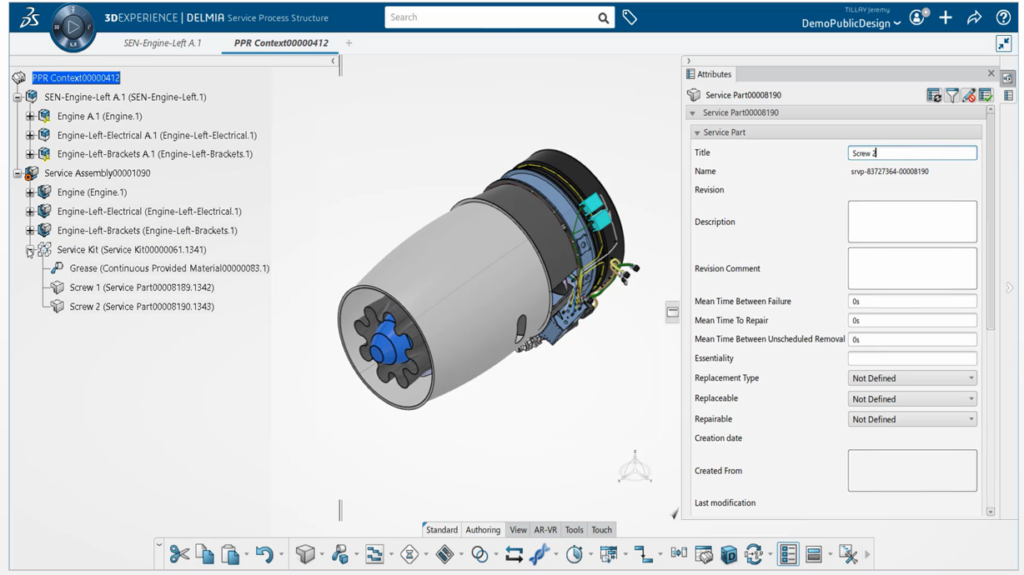
Define and Verify Service Processes
From here, a number of service processes can be defined and verified using 3D simulation. An interactive Gantt chart allows for quick and precise review of the tasks in each service or maintenance process. Analyzing and modifying the process plan is simple and visual.
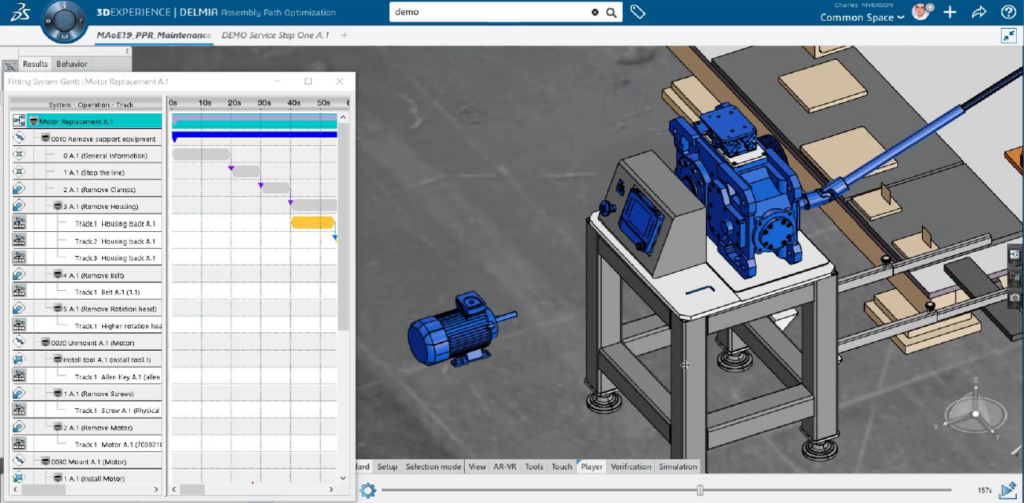
Create Work Instructions
Work instructions for the service or maintenance operations can be created using the 3DEXPERIENCE platform. These work instructions are created using the 3D data and enriched with operation-specific tools. A set of views can be defined to describe each step. These work instructions can then be published for execution in service manuals or service bulletins.
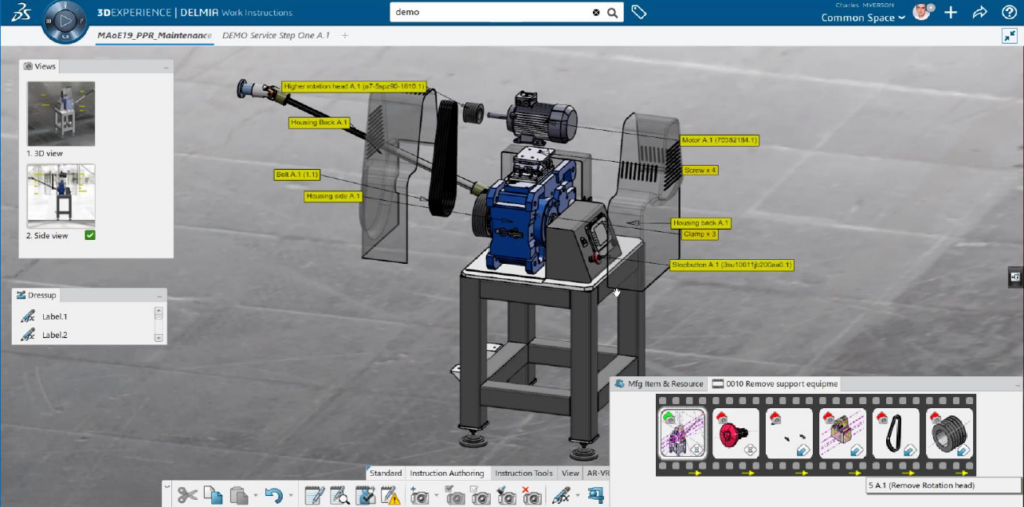
Analyze Maintenance Data
The 3DEXPERIENCE platform also provides tools for maintenance analysis. From this dashboard, you can access live data from the shop floor, use filters to refine the data, and identify equipment with high failure probability.
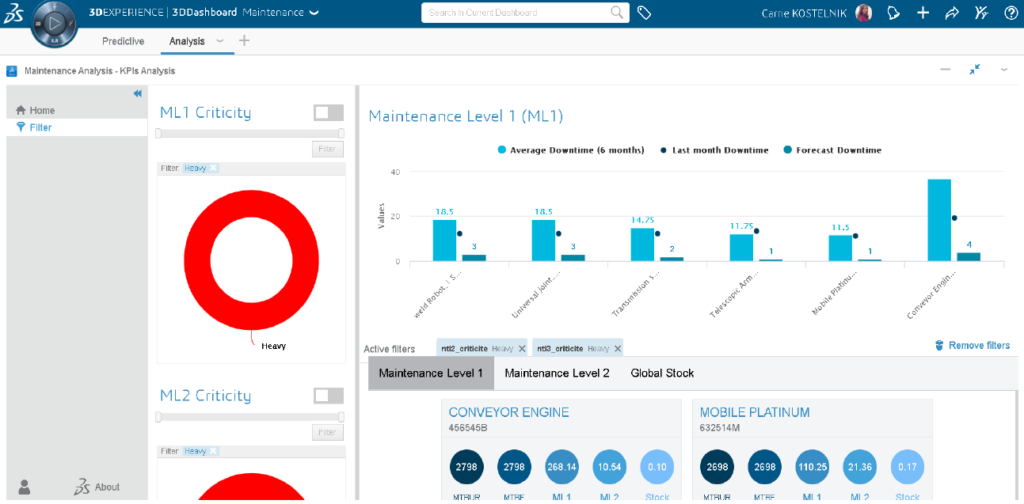
Teach Maintenance Operations Virtually
With virtual training, you can gradually teach the operator to perform the maintenance operations before the physical product exists. The operator can interact with the product and investigate the process. This life-like experience enables the operator to practice without risk of injury or defect.
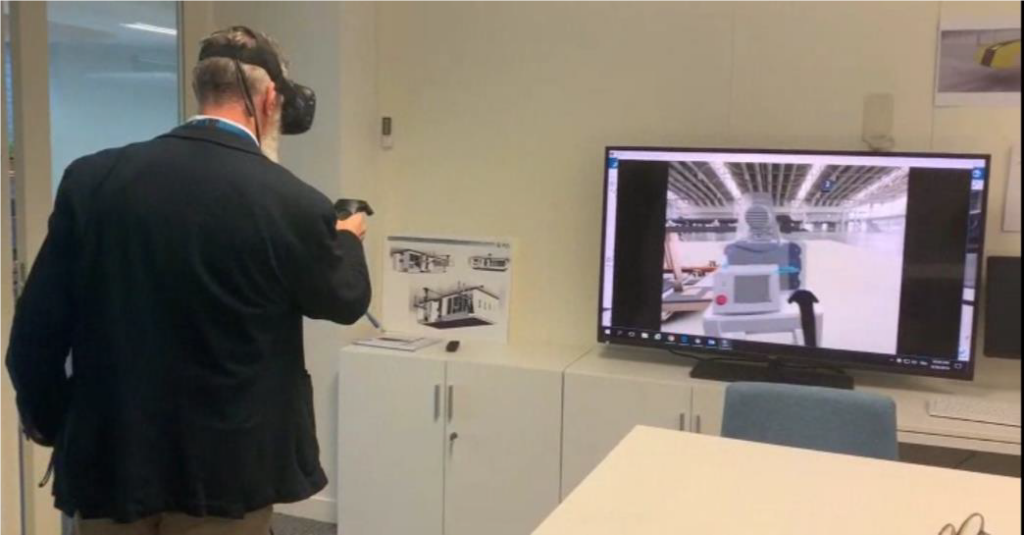
Optimize Overall Maintenance Cycle Times
You can see how the real world and the virtual world come together thanks to the 3DEXPERIENCE platform. With these tools, companies can optimize the overall maintenance cycle time by having a global system approach. On the 3DEXPERIENCE platform, all team members are collaborating concurrently to define and execute new processes.
Watch a short demo of DELMIA Service Process Engineer:
Questions?
If you have any questions or would like to learn more about the Service Process Engineer role on the Dassault Systèmes 3DEXPERIENCE platform, contact us at (954) 442-5400 or submit an online inquiry.